Кең жолақты ыстықтай таптау стандарының алдыңғы топ клеттеріндегі сығымдау режимдері


МАЗМҰНЫ
КІРІСПЕ 3
1 «АРСЕЛОРМИТАЛЛ ТЕМІРТАУ» 1700 ЫСТЫҚ ТАПТАУ ҮЗДІКСІЗ КЕҢ ЖОЛАҚТЫ СТАНЫ 4
1. 1 Үздіксіз құйылған жұқа слябты дайындамадан болат жолақтарды
өндірудің қазіргі кездегі шолу 4
1. 2 Дәстүрлі үздіксіз кеңжолақты орнақтарды ыстықтай таптау 5
2 КЕҢ ЖОЛАҚТЫ ЫСТЫҚТАЙ ТАПТАУ СТАНДАРЫНДА
ДЕФОРМАЦИЯЛАУ РЕЖИМДЕРІН ЕСЕПТЕУ 6
3 «1700» КЕҢ ЖОЛАҚТЫ ЫСТЫҚТАЙ ТАПТАУ СТАНЫНДА (КЖЫТС)
ТАПТАУ ПРОЦЕСІНІҢ ДЕФОРМАЦИЯЛЫҚ РЕЖИМІН ЕСЕПТЕУ 16
3. 1 Дайын өнімнің технологиялық сипаттамасы 16
3. 2 Сығымдау режимін есептеу 16
3. 3 Алдыңғы топ клеттеріндегі деформациялық режимді есептеу 17
3. 4 Артқы толассыз топ клеттеріндегі деформациялық режимдерді есептеу 30
4 СТАННЫҢ САҒАТТЫҚ ӨНІМДІЛІГІН ЕСЕПТЕУ 43
ҚОРЫТЫНДЫ 44
ҚОЛДАНЫЛҒАН ӘДЕБИЕТТЕР ТІЗІМІ 45
ҚОСЫМШАЛАР 48
КІРІСПЕ
Металлургия кәсiп орындарында таптау өндiрiсi көп жағдайда өндiрiстiк циклдардың шешушi сатысы болып табылады.
Таптау өнiмдерi халық шаруашылығының барлық салаларында, машина жасау өндiрiсiнде, құрылыс саласында, транспортта, энергетикада, авиакосмостық техникада және басқа да салаларда кеңiнен пайдаланылады.
Таптау бұйымдарының түрлерi (сортаментi) әрқилы. Олар - дөңгелек, квадрат, бұрыштық профильдер, швеллер, қоставрлы мәткелер, рельстер, қалың және жұқа қаңылтыр түрлерi, жолақты таптамалар, ленталар, тiгіссiз және пiсiрілген құбырлар, темiр жол доңғалақтары, қаңылтырдан майыстырып жасалған профильдер және тағы басқа арнаулы таптама профильдерiнiң түрлерi, егер әр профильдың ондаған геометриялық өлшемдiк түрлерi болатынын ескерсек, таптау профильдерiнiң мындаған түрлерi өндiрiледi.
Таптау процесiн жүргiзу кезiнде дайын бұйым өндiрумен қатар оның сапасын жақсарту, металл және энергия шығынын азайту, еңбек өнiмдiлiгiн арттыру мәселелерi де технологтар шешетiн негiзгi өзектi проблемалар қатарына жатады. Бұл проблемаларды түбегейлi шешуде қазiргi заманғы жаңа технологиялық процестердi пайдалану, таптау стандарының жетiлдiрiлген конструкциясын жасау, технологиялық процестердiң онтайландырған ең тиiмдi түрлерiн қолдану, комплекстi механикаландыру мен автоматтандыру жүйелерiн енгiзу, әсiресе, қазiргi заманғы технологиялық процестердi электронды есептеу машиналары негiзiнде автоматтандырылған реттеу және басқару жүйелерiн қолдану дайын бұйымның жоғары жылдамдықта өңдiрiлiп және оның жоғары сапалы болуын қамтамассыз етедi.
“Таптау өндiрiсiнiң технологиясы” пәнiн оқыған кезде таптау цехтарындағы технологиялық процестердi оқып - үйренумен қатар, деформациялық режимдерiн есептеу, бiлiктi калибрлеу және тағы басқа технологиялық режимдердi жобалау, техника - экономикалық көрсекiштердi, энергетикалық шығындардың дұрыс есептеу жолдарын да меңгеру негiзгi мақсатқа жататын проблемалар болып табылады.
1 «АРСЕЛОРМИТАЛЛ ТЕМІРТАУ» 1700
ЫСТЫҚ ПРОКАТТАУ ҮЗДІКСІЗ КЕҢ ЖОЛАҚТЫ СТАНЫ
1. 1 Үздіксіз құйылған жұқа слябты дайындамадан болат жолақтарды
өндірудің қазіргі кездегі шолу
Өткен ғасырдың соңғы 10 жылдығы жалпақ ыстықтай таптаудың таптау сапасын арттыру және өлшемдік сортаментінің кеңеюінің айқын үрдісі байқалады, бұл оны суықтай тапталған таптаудың орнына өнеркәсіптің түрлі салаларында тиімді қолдануға мүмкіндік береді [I] .
Ыстықтай тапталған болат өндірісінің дамуы технологиялық серпіліске - жұқа (қалыңдығы 50) үздіксіз құюдың бірыңғай желісі түрінде жаңа үлгідегі қаңылтырды таптау кешенін құруға алып келді. Бұл, біріншіден, жартылай өнімді құю процесін жетілдіру, соңғы өлшемдерге жақын, екіншіден, үнемділік пен өндірістік икемділікке объективті ұмтылу нәтижесі болып табылады. Жұқа қалпақты құю-таптау агрегаттарын (ЛПА) қолдану жоғары сапада шығарылатын өнімнің тоннасына күрделі және пайдалану шығындарын төмендету есебінен өндірістің тиімділігін айтарлықтай арттырады.
Дәстүрлі үздіксіз құю қондырғыларында, әдетте, қалыңдығы 250 мм-ге жуық слябтар алынады, олар ыстық күйінде 1, 5-20 мм қалыңдығына дейін алынады. Дайындаманың деформациясының жоғары дәрежесі қуатты жылжымалы құрамды және жоғары өндірістік шығындарды қажет етеді.
Құю технологиясын жетілдіру бірінші кезекте өндірістік тізбектен ең энергияны көп қажет ететін процестерді - дайындаманы таптау және қыздыруды болдырмау мақсатында дайындаманың қалыңдығын азайтуға бағытталған.
Үдерістің екі кезеңдерін неғұрлым тығыз байланыстыру бірлескен жұқа қақпақты құю-таптау агрегаттарында жүзеге асырылды, бұл келесі экономикалық артықшылықтарды алуға мүмкіндік берді:
- капитал салымдарын төмендету;
- өндіріс циклында металдың өту уақытын қысқарту;
- капиталдың айналымдылығын арттыру және қоймалық шығындарды азайту;
- шағын көлемді партиялардың үнемді өндірісін қамтамасыз ету;
- энергия шығынын төмендету.
Қазіргі уақытта жұқа слябтарды құюға арналған агрегаттардан ыстықтай басылған жолақтың сапасы дәстүрлі тәсілмен алынатын жолақтың сапасынан айырмашылығы жоқ. Жұқа слябтың таптау тапсырмасының оңтайлы шарттары арқасында аралас құю-таптау агрегатының тобына (жұқа слябтың барлық ұзындығы мен ені бойынша температураның біркелкі таралуы) дәстүрлі
технологияға қарағанда, тіпті ең жақсы жолақтың қалыңдығы, пішіні мен ені бойынша дәлдікке қол жеткізіледі [2] .
Жұқа слябтарды үздіксіз құю мен ыстық таптауды біріктірудің қазіргі заманғы технологиясы бастапқыда Еуропалық Одақ (ЕО) елдерінде құрылды, содан кейін бұл технология өнеркәсіптік енгізу барысында айтарлықтай жетілдірілді. ЛПМ конвертері бар және заманауи доғалы пештері бар технологиялық тізбекке жақсы үйлеседі. Соңғы артықшылық жазық таптауды
шығару үшін шағын зауыттарды құру шеңберінде жұқа слябтарға құю технологиясының тез таралуына ықпал етті. Дамушы елдердегі жаңа шағын зауыттар үшін JIIIM ерекше өзекті болып табылады. Қазіргі заманғы ЛИМ-нің өзіндік ерекшелігі барлық операцияларды автоматтандырудың жоғары деңгейі және дайындама құю және таптау.
Бүгінгі күні жалпы, сондай-ақ арнайы технологиялық және конструктивтік белгілері бар жұқа клябты ЛИД-лар мен шағын зауыттардың әр түрлі құрамдастары қолданылады.
Жетекші фирмалар жүргізген қарқынды зерттеулер нәтижесінде 90-жылдардың басында АҚШ, Германия және Жапония сияқты өнеркәсіптік дамыған елдерде жұқа слябтарды құю әдеттегі құбылыс болды. Дамушы елдерде технологиялық желілердің құрылысы басталды. 90-жылдардың басында осы бағытта жұмыстар жүргізе бастаған осы процесс пен фирманың келесі нұсқаларын атап өтуге болады:
- қалыңдығы 50 мм слябтарды "жұмсақ" қысусыз құю және одан әрі жолақтың соңғы қалыңдығына дейін ыстықтай таптау-Schloemann-Siemag фирмасының CSP процесі;
- қалыңдығы 50 слябты құю 90 мм, " жұмсақ " слябты сұйық өзегі бар кейбір аралық өлшемге дейін сығу және соңғы қалыңдыққа дейін таптау - Mannesmann Demag фирмасының ISP тәсілі, Danieli фирмасының TSC тәсілі және т. б. ;
- қалыңдығы 70 слябты құю . . . "Жұмсақ" қысусыз 150 мм, соңғы қалыңдыққа дейін кейінгі таптау - Voest - Alpine Industrieanlagenbau фирмасының CONROLL тәсілі, Tippins және Samsung фирмаларының TSP тәсілі, сондай-ақ Ipsco фирмасының кәсіпорнында ыстықтай тапталған жолақтар мен қалың қаңылтырды алу үшін орнату (Mannesmann Demag фирмасының әзірлеуі) .
1. 2 Дәстүрлі үздіксіз кеңжолақты орнақтарды ыстықтай таптау
Үздіксіз кең жолақты стан 1700 жолақтарды ыстықтай таптау үшін дәстүрлі болып табылады, ол қалыңдығы 1, 5-16, 0 мм және ені 750-1650 мм қалыңдығы 300 мм дейінгі құйма слябалардан табақты және рулонды таптай алуға мүмкіндік береді. ҮКЖС-1700 типтік сұлбасы 2. 1 - суретте көрсетілген. Слябаларды өндіру кезінде пеште 1200-1250°С дейін қыздырылады, одан әрі рольганг бойынша станның қара тобына тасымалданады. Таптаудан кейін алғашқы екі қара клеттерде жаю 25-50 мм қалыңдығына дейін үздіксіз үш клетті топқа түседі. Таза топтың алдында таптаудың алдыңғы және артқы ұштарын кесу үшін ұшпалы қайшылар орнатылған, бұл таптауды ұстап алу және тұрақтандыру кезінде динамикалық жүктемені азайтады. Алдыңғы ұшын кескеннен кейін жаюды таза қабыршақты сынғышқа жібереді. Бұдан әрі металды таза топта соңғы қалыңдыққа дейін таптайды. Жолақтардың соңғы геометриясын станның соңғы клеткасында орналасқан байланыссыз өлшеуіштермен өлшейді. Жолақтар үздіксіз таза топтан шыққаннан кейін оны бұрушы рольганг бойынша моталкаларға апарады. Бұрғыш рольгангте суыту жүйесі орналасқан, ол жолақтың температурасын 200-250°С төмендетеді.
1. 1 сурет - 1700 ҮКЖС жалпы сұлбасы
Бұл теріс құбылыстарды жою күйдіру режимдерін, желіаралық керуді, сондай-ақ прокатталатын жолақтардың температуралық режимін жетілдіру жолымен жүзеге асырылады. Жұқа жолақтарды прокаттауды оңтайландыру үшін келесі өзгерістер ұсынылады:
1. 4-ші, 5-ші және 6-шы клеттерде жеке қысуларды мәндерге қатысты 10-30% - ға азайту, демек, оларда ең жоғары түйіспелі кернеулердің 20-60-ға төмендеуі%;
2. Жеткізу температурасын 1080˚С дейін арттыру;
3. Бұл жолақтың қозғалыс тұрақтылығын арттыру есебінен оны таптау осіне жақсы ұстап тұруға ықпал етеді және жолақтардың әртүрлілігін азайтуға қосымша әсер етеді.
2 КЕҢ ЖОЛАҚТЫ ЫСТЫҚТАЙ ТАПТАУ СТАНДАРЫНДА
ДЕФОРМАЦИЯЛАУ РЕЖИМДЕРІН ЕСЕПТЕУ
Жолақ таптаманың қажетті түрін өндіру үшін өзара байланысты бірнеше мәселелерді шешу қажет. Олардың ең маңыздылары: алғашқы дайындама - сляб өлшемдерін анықтау; алдыңғы және соңғы топ клеттеріндегі сығымдау деңгейін анықтау; таптау процессінің жылдамдық, температуралық және энергокүштік параметрлерін есептеу.
Алғашқы дайындама - слябтың тиімді қалыңдығы жолақтың ақырғы қалыңдығына және стан клеттерінің сығымдау қабылеттілігіне байланысты анықталады. Сляб ені берілген жолақ енінен 20-30 мм-дей үлкенірек тағайындалады. Ал сляб ұзындығы қыздыру пешінің еніне байланысты қабылданады.
Вертикалдық тотықсындырғыш клетінде абсолюттік сығымдау 20-50 мм деңгейінде, ал горизонталдық тотықсындырғыш клетте салыстырмалы сығымдау деңгейі 5-20% шамасында тағайындалады. Сығымдау деңгейі бұдан төмен болса, сляб бетіндегі тотық қабыршағы толық сынбауы, ал тым жоғары болса, керісінше, татық қабыршағы металл бетіне тапталып кетуі мүмкін.
Алдың топтың негізгі деформациялаушы клеттерінде сығымдау шамасы біліктің тартып алу қабылетіне сәйкес анықталады. Ол үшін мына формуланы пайдаланады
α
2
Қmax
(2. 1)
мұндағы
- жұмыс білігінің минималдық радиусы (қажалған білік бетінің шекті қайыра жону мөлшеріне байланысты) ;
α Қmax - біліктің максималдық қармау бұрышы (рад. )
Өндірістік тәжірибеге сүйеніп болат біліктер үшін α Қmax =18-20 0 (0, 31-0, 35 рад), шойын біліктер үшін α Қmax =16-17 0 (0, 28-0, 30 рад) деңгейінде тағайындалады.
Универсалдық клеттердің вертикалдық біліктерінде сығымдау деңгейі шамамен 10-20 мм-дей болады яғни сол клеттің горизонталдық біліктерінде пайда болатын кеңею мәніне тең болады.
Максималдық қармау бұрышына сәйкес анықталған максималдық сығымдау мәнін одан әрі біліктің беріктігі арқылы немесе электрқозғағыш қуатының деңгейі арқылы да нақтылануы қажет. Ол үшін жұмыс клетінің білік беріктігіне сәйкес келетін таптау күшінің шекті мәні Р шек анықтау қажет.
Екі білікті дуо клеттері үшін бұл күш білік бөшкесінің беріктігіне сәйкес төмендегідей формула арқылы анықталады:
[P]
бөшке
=
(2. 2)
мұндағы
- білік майысуының шектікернеуі;
D- білік бөшкесінің диаметрінің минималдық мәні;
- білік бөшкесінің және мойнының ұзындығы; b- жолақ ені.
Кейбір жағдайда білік мойнының беріктігі білік бөшкесінің беріктігінен төмен болады, себебі білік мойнына таптау күшінің әсерінен туатын майысу кернеуімен қоса бұрау моментінен туатын бұрау кернеуі де үлкен әсер етеді. Сондықтан білік мойнының беріктігіне сәйкес шектеулі күшті де қоса анықтау қажет болады. Болат біліктер үшін:
[P]
мойын
=
(2. 3)
Шойын біліктер үшін
[P] мойын=
(2. 3′)
Мұндағы d - білік мойнының диаметрі;
- білік мойнының ұзындығы;
R- білік бөшкесінің радиусы;
(2. 4) - болат білік мойнына түсетін қосынды кернеу;
(2. 4′) - шойын білік мойнына түсетін қосынды кернеу;
Төрт білікті кварто клеттерінде аталған күштердің шекті мәні мына формулалармен анықталады;
[P]
бөшке
(2. 5)
[P]
мойын
=
(2. 5′)
Мұндағы D
on
, L
бөшке
- тіреу білігінің бөшке диаметрі және бөшке ұзындығы; d
on
,
мойын
- тіреу білігі мойын диаметрі және ұзындығы.
Келтірілген (2. 2), (2. 4), (2. 4′), (2. 5) және (2. 5′) формулалардағы білік майысуының ұлақсат етілген шекті кернеуінің
мәнін білік материалының сапасына сәйкес мынадай деңгейде (1 кесте) тағайындайды.
2. 1 кесте

Шойын
Легірленген шойын
Болат құйма
Жоғарыкөміртекті шыңдалған болат
Легірленген шыңдалған болат
70-80
80-90
100-120
120-130
140-150
Ал шекті бұрау кернеуінің (
) мәні шойын біліктер үшін 70-80 МПа, болат біліктер үшін 80-100 МПа деңгейінде тағайындалады.
Барлық өтулерде туатын нақты таптау күші Р т білік беріктігін қамтамасыз ететін шекті күштің мәнінен аспауы керек, яғни
Р т ≤ [P] ; (2. 6)
Мұндағы [P] - білік мойны беріктігінің, немесе білік бөшкесі беріктігінің формулалары арқылы есептелген шекті күштердің ең төменгі (минималды) мәні.
Таптау күшінің
Р=
(2. 7)
Формуласы арқылы есептелетінін ескерін, сығымдау мәнінің білік беріктігіне сәйкес максималдық шамасын (6) формуладан анықтауға болады, яғни
бұдан
(2. 8)
Мұндағы
түйісу бетіндегі орташа нормальдық кернеу. Оның мәні М. Е. Бровман, А. И. Целиков және басқа да авторлардың белгілі формулалары арқылы есептеледі. Алайда
-дің мәні өз кезенінде абсолюттік сығымдау шамасына тәуелді болғандықтан,
мәнін итерация әдісімен есептеуге тура келеді.
Білік пен деформацияланушы металл арасындағы түйісу бетінде туатын орташа нормальдық кернеудің
мәні металдың ақыштық шегінің
деңгейіне және деформация ауқымының пішіндік факторына
тәуелді болады. Егер деформация ауқымының пішіндік факторы
<0, 5 болса, онда
Целиков-Смирнов формуласымен есептеледі:
(2. 9)
Деформация ауқымының пішіндік факторы 0, 5<
<2 арлығында болса, р
ср
Бровман формуласы арқкылы есептеледі:
(2. 10)
Егер
>2 онда
Бровманның екінші формуласы арқылы есептеледі:
(2. 11)
Металдың аққыштық шегі, немесе деформациялауға кедергісі
ыстықтай таптау процестерінде «термомеханикалық коэффициентер» әдісін [1] қолдану негізінде (Третьяков-Зюзин-Бровман әдісі) мына формула арқылы анықталады:
; (2. 12)
Мұндағы
- металдың базистік аққыштық шегі, МПа,
және
- температуралық, деформациялық және жылдамдық коэффициентері. Бұлардың мәні металл маркасы, таптау температурасы, салыстырмалы сығымдау көрсеткіші және деформациялау жылдамдығына сәйкес әрбір өту кезінде әдеби анықтағыштан [1] алынады.
Өндірістік жағдайда таптау станының басты электрқозғағышының қуаты жетімсіз болуы мүмкін (мұндай жағдай ескі стандарда және деформацияға кедергісі жоғары легирленген болаттан алынатын жолақты таптау кезінде кездеседі) . Сондықтан әрбір өтудегі абсолюттік сығымдау деңгейін электрқозғағышының валына түсетін бұрау моментінің немесе қуатының шектеулі шамасы арқылы анықтайды. Ол үшін алдымен білік бөшкесінде деформация кезінде пайда болатын таптау моментін М тап , білік мойнында туатын үйкеліс моментін М үйк1 , беріліс механизмдерінің валдарында туатын үйкеліс моментін М үйк2 , деформациялау процесінсіз біліктер бос айналын тұрғанда туатын моментін М бос және білік айнымалы жылдамдықпен жұмыс жасағанда туатын динамикалық моментін төмендегідей формулалармен есептеу керек.
М
тап
=
(2. 13)
М
үйк1
=
(2. 14)
М
үйк2
=
(2. 15)
М бос =0, 05М ном. эл-қозғ (2. 16)
М
дин
=
(2. 17)
Мұндағы М тап - білік бөшкесінде туатын бұрау моменті, бұл момент деформациялау ауқымында металды таптауға шығын болатын пайдалы момент; М үйк1 - білік мойнындағы үйкеліс кедергісін жеңуге жұмсалатын бұрау моменті; М үйк2 - беріліс механизмдері валдарының мойнында туатын үйкеліс кедергісін жеңуге кететін бұрау моменті; М бос - біліктер металсыз бос айналғанда пайда болатын қосалқы бұрау моменті және М дин - біліктер айнымалы жылдамдықпен жұмыс істегенде туатын инерция күштерінің кедергісінен туатын бұрау моменті.
Осы бұрау моменттерінің барлық кедергісін станның басты электрқозғағышының валында пайда болатын келтірілген момент жеңеді, яғни электрқозғағышының валында туатын келтірілген момент төмендегі формуламен есептеледі:
М
эл. қозғ.
=
(2. 18)
Мұндағы
(2. 19)
М′
үйк1
=
(2. 20)
М′
үйк2
=
(2. 21)
М′ бос =0, 05 М ном. эл. қозғ. ; (2. 22)
М′
дин
=
(2. 23)
иін коэф-ті; (2. 24)
f мойын - білік мойнындағы үйкеліс коэффициенті.
d мойын - білік мойнының диаметрі;
- станның пайдалы әсер коэффициенті;
=0, 75÷0, 95;
М ном. эл-қозғ. - электроқозғағышының номиналдық моменті (құжатында келтірілген) .
М
ном. эл-қозғ.
=
(2. 25)
J- электрқозғағышы валына келтірілген инерция моменті.
бұрыштық үдеу мәні;
Осылай есептелген электрқозғағышы валына түскен келтірілген бұрау моменті таптау процесінің кез-келген өтуі кезінде төмендегідей теңсіздіктен аспауы қажет.
М эл. -қозғ. ≤[К·М ном. эл. қозғ. ] ; (2. 26)
К=2, 5÷2, 75
Реверсивті станда динамикалық момент жоғары деңгейде болуына байланысты электрқозғағыш элементтерінің орамдарының тез қызып кетпеуі үшін есептелген М эл. қозғ. ≤ М ном ; (2. 27) болуы керек.
Алдыңғы топ клеттеріндегі жиынтық салыстырмалы сығымдау көрсеткіші барлық клеттердегі қосынды сығымдаудың 70-90%-ін қамтуы керек, ал қалған 10-30% сығымдау артқы топ клеттерінің үлесінде болады.
Алдыңғы және артқы топ клеттеріндегі сығымдау деңгейінің мұндай ара қатынасының болуы, біріншіден, алғашқы топ клеттерінде таптау кезінде металл температурасы жоғары деңгейде болуына байланысты деформация қарқыныда жоғары болуы керек (металл кедергісі төмен болғандықтан), екіншіден, осындай қалыптасқан сығымдау деңгейдерінің болуы-алдыңғы және артқы топ клеттерінде таптау циклінің өзара теңдігін қамтамасыз етеді (таптама ұзындығының өзгеруіне сәйкес) .
Деформациялық режимді есептеудің тағы бір маңызды бөлігі - металдың әр өтудегі температурасының өзгеруін есептеу.
Алдыңғы топ клеттеріндегі металл температурасының төмендеуін Иванцов т. п. формуласымен анықтауға болады:
; (2. 28)
Мұндағы t- таптаманың алдыңғы өтудегі температурасы, 0 С ; ε- алдыңғы өтудегі таптау уақыты және ол өту аяқталғаннан келесі өту басталғанға дейін қажет болатын үзіліс уақытының қосындысы, сек; h 0 - таптаманың алдыңғы өтуден кейінгі немесе осы өту алдыңғы қалындығы, мм.
Методикалық пеште қажетті деңгейге қыздырылған сляб (болат маркасының химиялық құрамына сәйкес) алдыңғы топ клеттеріне рольганг арқылы жіберіледі және бұл топтың әрбір клетінде металл бір рет қана өтеді және кез-келген таптау кезеңінде таптама тек бір ғана клетте деформацияланады. Таптаманың әрбір өтуден кейін ұзару мөлшеріне сәйкес әрбір көршілес клеттердің ара қашықтығы да біртіндеп алыстатылып орналасқан. Ал артқы топ клеттерінде әрбір таптама барлық клеттерде бір мезгілде деформацияланады, себебі бұл топта таптау процесі толассыз режиммен жүргізіледі.
Осыған байланысты бұл топтағы клеттер бір-бірімен тіркес орналасады және бір-бірімен ара қашықтығы 5-6 метрден аспайды. 2. 1 кестеде қазіргі заманғы кең жолақты толассыз ыстықтай таптау стандарының алдыңғы топ клеттеріндегі қалыптасқан салыстырмалы сығымдау режимдерінің тиімді деңгейлері көрсетілген.
2. 1- кесте. Кең жолақты ыстықтай таптау стандарының алдыңғы топ клеттеріндегі сығымдау режимдері
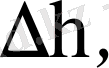
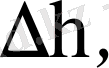
Бұл келтірілген сығымдау деңгейлері әрбір өтуге қойылатын шектеулерді (біліктің тартып алу қабылеті, біліктің беріктігі және электрқозғағышының қуаты) толық қамтамасыз етеді.
Артқы толассыз клеттер тобында деформациялау режимі жоғарыда айтылған шектеулерді қамтамасыз етуі қажет және өндірістік мәліметтерді де есепке ала отырып жүргізу керек;
2. 2-кестеде кең жолақты ыстықтай таптау стандарының ақырғы топ клеттеріндегі өндірістік жағдайда анықталған сығымдау режимінің тиімді деңгейлерінің мөлшері келтірілген.
- Бұдан кейін толассыз таптауды қамтамасыз ететін жылдамдық режимі есептеледі;
- Әр клеттегі температуралық режим есептеледі;
- Деформациялау процесіндегі әр клеттегі күш, моменттер және энергия - қуат шығындары есептеледі;
- Алынған нәтижелер қажет болса қосалқы есептеледі, нақтыланады.
Тағы бір есте болатын жағдай-толассыз ақырғы топтың соңғы екі кілетінде дайын бұйым сапасын жақсарту мақсатында сығымдау деңгейлері аз мөлшерде тағайындалады, бірақ ең ақырғы клеттегі сығымдау деңгейі 8% тен кем болмауы керек, әйтпесе, таптау соңынан суыту кезінде металл түйіршіктері өте ірі өсіп кетеді де дайын бұйымның механикалық қасиеттері төмендеп кетеді.
Әр өтудегі сығымдау режимі қандай шектеуге тәуелді болуына байланысты әрбір клеттегі қуат жүктелуінің деңгейі әртүрлі сипатты болады.
2. 1-суретте артқы топ клеттерінде қолданылатын электрқозғағыштарының қуат жүктелуінің өндірісте кездесетін варианттары келтірілген.
Бұл суреттегі 2. 1-график электрқозғағыш қуаты сығымдау режимін жектеген кезде қолданылады; бұл жағдайда алғашқы 5-клеттің электрқозғағышның қуаты максималдық деңгейде пайдаланылады.
2. 2-график жектеуші фактар білікке түсетін күш деңгейі болса қолданылады, бұл жағдайда алғашқы 5 клетте таптау күші тұрақты болуы қажет, сондықтан таптау жылдамдығының өсуіне байланысты әрбір келесі клеттің электрқозғағышының қуат жүктелуі өседі;
2. 3-график пластикалық қасиеті төмен болат маркаларын таптау кезінде қолданылады, себебі, әрбір келесі клетте сығымдау деңгейін күрт төмендету қажеттігі туады, сондықтан таптау күші де және қозғағыш қуаты да төмендейді.
... жалғасы- Іс жүргізу
- Автоматтандыру, Техника
- Алғашқы әскери дайындық
- Астрономия
- Ауыл шаруашылығы
- Банк ісі
- Бизнесті бағалау
- Биология
- Бухгалтерлік іс
- Валеология
- Ветеринария
- География
- Геология, Геофизика, Геодезия
- Дін
- Ет, сүт, шарап өнімдері
- Жалпы тарих
- Жер кадастрі, Жылжымайтын мүлік
- Журналистика
- Информатика
- Кеден ісі
- Маркетинг
- Математика, Геометрия
- Медицина
- Мемлекеттік басқару
- Менеджмент
- Мұнай, Газ
- Мұрағат ісі
- Мәдениеттану
- ОБЖ (Основы безопасности жизнедеятельности)
- Педагогика
- Полиграфия
- Психология
- Салық
- Саясаттану
- Сақтандыру
- Сертификаттау, стандарттау
- Социология, Демография
- Спорт
- Статистика
- Тілтану, Филология
- Тарихи тұлғалар
- Тау-кен ісі
- Транспорт
- Туризм
- Физика
- Философия
- Халықаралық қатынастар
- Химия
- Экология, Қоршаған ортаны қорғау
- Экономика
- Экономикалық география
- Электротехника
- Қазақстан тарихы
- Қаржы
- Құрылыс
- Құқық, Криминалистика
- Әдебиет
- Өнер, музыка
- Өнеркәсіп, Өндіріс
Қазақ тілінде жазылған рефераттар, курстық жұмыстар, дипломдық жұмыстар бойынша біздің қор #1 болып табылады.

Ақпарат
Қосымша
Email: info@stud.kz