Материалдың қаттылығын өлшеу әдістері


Мазмұны
Кіріспе 4
1. Қаттылықтың негізгі түсініктері 5
1. 1. Қаттылықтың сипаттамасы және анықтау әдістері 6
2. Материалдың қаттылығын өлшеу әдістері 7
2. 1. Статикалық әдіс бойынша 7
2. 1. 1. Бриннел әдісі 7
2. 1. 2. Роквелл әдісі 11
2. 1. 3. Виккерс әдісі 15
2. 2. Динамкалық әдіс бойынша. . 18
2. 2. 1. Шора бойынша қаттылық (басып енгізу әдісі) . . 18
2. 2. 2. Кері серпіліс әдісі (Шора бойынша) 19
2. 2. 3. Тырнау арқылы қаттылыққа сынау 21
Қорытынды 24
Әдебиеттер тізімі . . . 25
Кіріспе
Металлдар мен құймалардың сапасын анықтайтын әртүрлі құрылыста және әр түрлі жұмыс жағдайларында қолдануға мүмкіндік беретін кең таралған сипаттамалардың бірі қаттылық болып табылады. Металлдардың беріктік, салыстырмалы ұзару және т. б. басқа механикалық сипаттамаларына қарағанда қаттылыққа сынау көп қолданылады.
Адамзат қоғамы материалды қандай күйде болмасын, қаттылыққа сынауды өте ертеден бері қолданып келеді. Осылайша, металл тиындарының нағызынан жасандысын айыру үшін «тістеп тексеру» әдісі ежелгі кездегі археологиялық және әдеби мұралардан белгілі. 1722 ж. Ремюр алғаш болып материалдың қаттылығына ғылыми-зертханалық сынақтар жүргізді, ал 1901 ж. қаттылыққа сынау - материалдың механикалық қасиеттерін анықтау әдісі ретінде Бриннеллдің жұмыстары шыққаннан кейін ғана жалпыға танылды.
Қаттылықты өлшейтін әдістер екі негізгі категорияға бөлінеді: қаттылықты анықтаудың статикалық әдісі және қаттылықты анықтаудың динамикалық әдісі.
Ең көбірек танылған түрі - статикалық әдіс. Мұнда индикаторға берілетін жүктеме біртіндеп және аз-аздап қосылады да, жүктеме беруге кететін уақыт сол әдістің стандарттарына сәйкес болады.
Ал қаттылықты анықтаудың динамкалық әдісінде сыналушы индикатор үлгіге серпімді беріліс және әр түрлі шығындар (діріл, жылу бөлу, үйкеліс және т. б. ) жасайтын белгілі бір кинетикалық энергиямен әсер етеді. Қаттылық бұл жерде индикаторды кинетикалық энергиясының шығынын бағалау негізінде анықталады. Динамикалық қаттылықты көп жағдайда материалдың соғылуы кезіндегі қаттылығы деп атайды. Динамикалық әдіске шартты түрде тырнау әдісін жатқызуға болады.
Қаттылықты құралмен анықтауда твердомер деп аталатын аспап қолданылады. Обьектке әсер ету сатысына байланысты қаттылықты анықтау әдісі бұзатын әдіске де, бұзбайтын әдіске де жатуы мүмкін.
Нақты қаттылықты анықтау әдісі материал қасиетіне, өлшеу мақсатына, оны өткізу жағдайына және қолда бар аспапқа байланысты таңдалады.
- Қаттылықтың негізгі түсініктері
Металдың ең негізгі механикалық қасиеттерінің бірі ол қаттылық болып табылады, ал металдың басқа қасиеттері онымен өте тығыз байланыста болады. Демек, металдың қаттылығын біле отырып, оның басқа да механикалық қасиеттерін металды бүлдірмей оңай анықтауға болады. Металдардың механикалық қасиеттері тәжірибе жүзінде арнайы сынаушы машиналардың жәрдемімен анықталады. Механикалық сынау әдісінде металдар созу, ию, соғу, қажыту арқылы сыналады [1] .
Қаттылық мынаған байланысты:
- Автомаралық қашықтыққа.
- Координациондық санға - сан жоғары болған сайын, соғұрлым қаттылықта жоғары; кристаллдағы жақын теңжойылған бірдей бөліктердің (ион немесе атом) санын анықтайтын сипаттама.
- Валенттілікке - химиялық элемент атомдарының басқа элемент атомдарымен химиялық байланыстың белгілі санын түзу қасиеті.
- Химиялық байланыс табиғатына - жүйенің толық энергиясының азаюымен бірге жүретін, байланысатын бөліктердің электронды бұлттарының жабылуына негізделген атомдардың әрекеттесу құбылысы.
- Бағытына (мысалы, дистен минералы - оның қаттылығы кристалл айналасында 4, ал көлденеңнен - 7)
- Нәзіктік пен соққылық. Нәзіктік - материалдың көрінетін қалдық деформациясыз бұзылу қасиеті. Соққы - металл мен құймалардың соққыға және тағы басқа қысыммен өңдеу түрлеріне ұшырау қасиеті (прокаттау, сүйрелеу, пресстеу, штамптау) .
- Иілгіштік - минерал оңай иіледі, қайта орнына келмейді. (мысалы, тальк - минерал, кристаллды зат. Ақ түсті (кейде жасыл) майлы борпылдақ ұнтақ.
- Серпімділік - минерал майысады, бірақ қалпына келеді (мысалы, слюда - қабатты құрылымды алюмосиликат тобының минералы. Слюда - интрузивті, метоморфты және таулы тұнба текті кең таралған текті түзуші минерал, сонымен қатар маңызды, қажетті қазба.
- Тұтқырлық - минералды сындыру қиын (мысалы, жадеит (нефрит) - сілтілі моноклинді пироксен, натрий силикаты және алюминий топтарының жасыл түсті минералы)
- Жабысқақтық - жазық паралелді беткей түзумен арнайы кристаллографикалық бағытта жарылу қасиеті.
- Қазіргі кезде бар материалдардың ішіндігі ең қаттысы көміртегінің екі аллотропты модификациясы - лонсдейлит, алмаз бен фуллерит қаттылығынан 58% асып түседі. Бірақ бұл заттарды тәжірибеде қолдану әзірге мүмкіндігі төмен. Таралған заттардың ішіндегі ең қаттысы алмаз (Моос шкаласы бойынша 10 бірлік) . [6] Қаттылықтың сипаттамасы және анықтау әдістері
Қаттылық - материалдың өзінен де қатты дененің енуіне қарсы тұру қасиеті, сонымен бірге қаттырақ дененің басқа материалға ену қасиеті. Қаттылық материалдың бұзыла бастауы үшін қажетті қүш өлшемімен анықталады. Салыстырмалы және абсолютті қаттылықты айырады. Салыстырмалы қаттылық - бір материалдың басқамен салыстырғандағы қаттылығы, маңызды диагностикалық қасиет болып табылады. Абсолютті - ол аспаптық - майысу әдісімен өлшенеді [1, 2] .
Қаттылықты анықтау үшін материал беткейіне арнайы күшпен болаттық шар, алмазды конус, пирамида және ине түріндегі затпен майыстыра басу. Беткейінде қалатын таңбаның өлшеміне қарап материал қаттылығын анықтайды. Осылайша, қаттылық материалдың өзінен қатты денені - иденторды енгізгенде пайда болатын жергілікті пластикалық деформацияға қарсы тұру қасиеті. Материалдың қаттылығын өлшеу тәсіліне байланысты санды түрде Бринелл (НВ), Роквелл (HRC) немесе Виккерс (HV) бойынша қаттылық сандарымен сипаттайды [5] .
Аталған әдістердің әрқайсысының өздерінше кемшілігі және артықшылығы бар, сондықтан ыңғайына байланысты олардың барлығы да кеңінен қолданылады.
Металдар мен қоспалардың қаттылығы жұмсақ немесе орта мөлшерде болғанда, Бринелл әдісі қолданылады. Егер металдардың қаттылығы тым жоғары болса, онда Виккерс әдісі бойынша анықталады. Бұл екі әдіс бір-біріне өте ұқсас және ортақ кемшілігі: біріншіден, шариктің (пирамиданың) орны үлгіде қалып қояды, екіншіден, таңбаның (айшықтың) ауданын анықтау өте ыңғайсыз.
Металдарды жаппай сынау кезінде бұл әдістер қиындау, сондықтан Роквелл әдісі кеңінен қолданылады. Роквелл әдісімен жұмсақ және қатты металдардың қаттылығын айшықтың ауданын өлшемей-ақ бірден прибордың шкаласы арқылы анықтайды.
Ұштықтың әсер етуіне байланысты қаттылықты өлшеудің бірнеше түрін ажыратады. Қаттылықты индентормен басу арқылы, шар ұшымен секіртіп ұру арқылы қаттылықты өлшеуге болады. Тырнау арқылы анықталған қаттылық бұзылуға қарсылықты сипаттайды, секірту арқылы - серпімділік қасиетін, басып майыстыру - пластикалық деформацияға қарсылықты сипаттайды.
2 Материалдардың қаттылығын өлшеу әдістері
2. 1 Статикалық әдіс бойынша
2. 1. 1 Бринелл әдісі бойынша қаттылықты анықтау
Бринелл әдісі - қаттылықты металлдық шар қалдыратын таңба диаметрі бойынша анықтау. Қаттылық дақ ауданының шарға жұмсаған күш қатынасына тең, Бринелл бойынша өлшем бірлігі Па (кгс/мм²) . ГОСТ 9012-59 бойынша Бринелл бойынша қаттылық саны өлшем бірліксіз жазылады. Бұл әдіс бойынша анықталған қаттылық НВ деп белгіленеді, мұнда H = hardness (ағыл. қаттылық), B - Бринелл [1] .
Бринелл әдісімен металлдың қаттылығын анықтау үшін оған шынықтырылған болат шарикті (НV= 850) белгілі күшпен батырады. Бринелл машинасының диаметрі 2, 5; 5; 10 мм үш түрлі шарикпен жабдықталған. Металдың қаттылығын Бринелл әдісі бойынша анықтау сұлбасы 2. 1 суретте көрсетілген.
Металдың қаттылығы мен қалыңдығына байланысты (2. 1 кесте), шарикпен машинаның үстеліне қойылған үлгіге күш түсіріліп, сол күштің әсерінде шамалы уақыт ұсталғаннан кейін үлгі машинадан алынады. Нәтижесінде сыналған үлгінің бетінде шариктың таңбасы (айшық) қалады. Неғұрлым металл жұмсақ болса, соғұрлым үлгіге шарик тереңірек батады. Қаттылық үлгіге түсірілген күштің, үлгіде қалдырылған шарик таңбасының бет ауданына қатынасымен анықталады. Бринелл әдісі бойынша анықталған қаттылық НВ әрпімен белгіленіп, мына формула бойынша есептеліп шығарылады:
,
(2. 1)
Мұндағы Р- үлгіге түсірілген күш, кГс;
S = π·D·h- шариктің үлгідегі таңбасының ауданы, мм 2 ;
D - шариктің диаметрі, мм ;
h - айшықтың тереңдігі, мм;
d - айшықтың диаметрі, мм;
. (2. 2)
Металдың қаттылығы мен қалыңдығына байланысты 2. 1-кестесін қолдана отырып, шариктің диаметрін және оған түсірілетін күшті (Р) анықтайды, сонымен қатар күштің шарикке түсу уақыты да көрсетілген. Күшті (Р) металдың маркаларына байланысты мына формула арқылы анықтаймыз:
Қара металдар мен олардың қорытпалары үшін Р= 30 · D 2 ;
Қола, мыс, жез үшін Р= 10 ·D 2 ;
Алюминий, подшипник қорытпалары үшін Р= 2, 5 · D 2 [8] ;
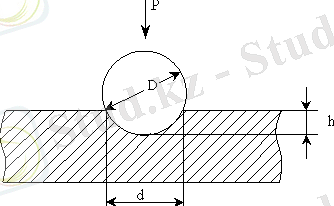
2. 1- сурет. Бринелл бойынша қаттылықты анықтау схемасы.
2. 1- кесте
60 . . . 230
230 . . . 700
700 ден жоғары
Болат шарик
Алмаз конус
Алмаз конус
100/1000
150/1500
60/600
В
С
А
HRB
HRC
HRA
25 . . . 100
20 . . . 70
70 . . . 85
2. 2 - кесте. Металдардың қалыңдығына байланысты шариктің диаметрін, металдарға түсетін күшті және уақыт мөлшерін анықтау.
Металдың қалыңдығы,
мм
2 ден кем емес
2 . . . 4
3 . . . 6
2, 5
5
10
187, 5
750
3000
3 тен кем емес
3 . . . 6
6 дан жоғары
2, 5
5
10
62, 5
250
1000
2 ден кем емес
2 . . . 4
3 . . . 6
187, 5
750
3000
3 тен кем емес
3 . . . 6
6 . . . 9
2, 5
5
10
62, 5
250
1000
3 тен кем емес
3 . . . 6
6-дан
жоғары
2, 5
5
10
15, 6
62, 6
250
Шариктың із таңбасын дұрыс түсіру үшін сыналатын металл үлгісінің беті бір қалыпты тегіс болу керек.
Сыналатын металдың қалыңдығы таңбасының тереңдігіне қарағанда 10 есе үлкен, ал диаметрі d ≈ (0, 2 . . . 0, 6) D болуы керек [6] .
Бирнелл әдісі бойынша металлдардың қаттылығын өлшеу үшін қолданылатын аспаптар:
- Жартылай автоматты аспаптар ТБ 5004, ТБ 5004-03.
Аспаптар металлдар қаттылығын екі режимде өлшеуге арналған:
- ГОСТ 9012 сәйкестілігімен Бринелл әдісі бойынша, айшық диаметрін аспап құрамына кіретін жарықтандырғышы бар микроскоп МПБ-3 (2. 2- сурет) көмегімен өлшеу. Әдетте, диаметр таңбасының (айшық) дәл өлшемi үшiн екi объективте 50-еселi үлкею және 25-еселi үлкеюге комплект жасайтын микроскоп МбП-3 өлшеуішін қолданады.
- - сурет. МБП-3 өлшеуіш микроскобы
- Сілтеуіші бар қондырылған тілді индикатор (ТБ 5004), немесе санды көрсеткіші және нәтижені математикалық өңдеуі бар электрондық блогы бар электрондық датчик.
2) Портативті аспап ТБП 501 (2. 3-сурет)
Бұл аспап Бринелл әдісі бойынша металдардың қаттылығын өлшеуге арналған. Қазіргі таңда цехта және машинажасау, металлургиялық өнеркәсіп зертханаларында, сонымен қатар ірі және тасымалданбайтын өнімдердің қаттылығын өлшейтін жерлерде, қоймаларда, базаларда қолданылады.
2. 3-сурет. Бринелл әдісі бойынша мелалдардың қаттылығын өлшеуге арналған портативті аспап ТБП 501
Аспап қозғалмалы саналғанымен, ол көбіне тұрбалар материалының үлгілер мен бөліктердегі қаттылықтың тұрақты өлшемдері үшін алынады. Салмағы 20 кг. Қаттылықты өлшеу диапазоны 8 . . . 450НВ, сыналатын жүктемелер 1839, 2452, 4903, 7355, 9807, 14710, 29420Н. Сыналатын жүктемелер шегі ±1%. Аспап диаметрлері 1, 588; 3, 175; 5; 6, 35; 10; 12, 7 мм инденторлар - шарлармен жүзеге асырылады.
Аспаптың негізгі бөлiгi - корпус 1 болып табылады, оның iшiнде сынау жүктемесiн өзі қабылдайтын пластина бекiтілген. Корпустың 1 iшiнде орналасқан жүктемелі бұранда серпiмдi қыздырып өңделген құрыштан жасалған тұтқамен 2 жалғанған, оның астынғы жағында сынау ұшы 3 орнатылған. Тұтқаның iшiнде көрсеткіштің механизмі 4 және сағат типтес индикатор 5 бекітілген, ол үлгiге тiркелген жүктемені қосалқы өлшеу үшін қызмет етеді. Күштi азайту үшiн корпуста 6 орналасқан саптағы тегершіктер қызмет атқарады. Бекітілген тіреуде 7 орналасатын материалдың сыналатын бөлігін тұтқаның 2 ұшына 3 бекітілген шарға көтергіш бұрандамен 8 қысады да, алып-салмалы саптың 9 айналуымен күшті механизмнің 4 көмегімен серпімді тұтқаға 2 береді де, шарды үлгіге басып қысады. Бұл кезде тұтқа үлгі үстіне қалыпты әрекет ететін күшке пропорционалды серпімді деформацияланады. Бұл деформация индикатормен 5 өлшенеді [2] .
2. 1. 2 Роквелл әдісі бойынша материалдың қаттылығын анықтау
Роквелл әдісі - зерттелетін материал беткейіне металлдық немесе алмаздық конусты басу тереңдігіне негізделген. Бұл әдіс бойынша анықталған қаттылық өлшемсіз және HR, HRB, HRC и HRA болып белгіленеді; қаттылық HR = 100 - kd формуласымен есептелінеді, мұнда d -негізгі күшті алғаннан кейінгі басылу тереңдігі, ал k - коэффициент. Осылайша Роквелл бойынша максималды қаттылық HR 100 тең [2, 5] .
Роквелл әдісі бойынша өлшеуді жүргізу мен қаттылық санын анықтау ГОСТ 9013-59 регламенттеледі.
Сыналатын металл үлгісінің бетіне төбесіндегі бұрышы 120 0 тең, алмаздан жасаған конус немесе диаметрі 1, 59 мм шынықтырылған болаттан жасаған шарик белгілі күшпен батырылады, алдындағы әсер ететін күштің мәні - Р 0 (2. 4, а - суреті) және соңғы рет әсер ететін күштің мәні- Р 1 (2. 4, б- сурет) . Барлық жағдайда алдын ала түсетін күш Р 0 = 10 кгс-қа тең болады, ал соңғы рет (кейін түсетін) күш Р 1 , металдың материалына байланысты өзгеріп отырады, сондықтан жалпы шарикке немесе конусқа түсетін күш Р = Р 0 + Р 1 төмендегідей болып анықталады;
- шыныққан болат шарикті (d = 1, 588 мм ) үлгіге батырғанда ақтық күш Р 1 = 90 кгс (900 Н), онда жалпы күш Р = Р 0 + Р 1 = 100кгс. Бұл жағдайда металдың қаттылығын аспаптың В шкаласы анықтайды;
- алмаз конусты үлгіге батырғанда ақтық күш Р 1 = 140 кгс (1400Н), ал жалпы күш Р = Р 0 + Р 1 = 150кгс (С шкаласы) ;
- алмаз конусты үлгіге батырғанда Р 1 = 50кгс (500Н) , ал Р = Р 0 + Р 1 = 60кгс (А шкаласымен металдың қаттылығы анықталады) .
Металдың қаттылығы айтылған әдісте бірден Роквелл аспабының индикатор шкаласымен анықталады. Индикаторда үш шкала қатар орналасқан (А, В, С шкаласы) .
Егер де сыналатын металл өте қатты және морттық қасиеті жоғары болса, онда олардың қаттылығы А шкаласы (қара түсті) бойынша анықталады немесе келесі формуламен есептейді:
. (2. 3)
С шкаласы (қара түсті) бойынша көп көміртекті болаттар мен қорытпалардың қаттылығын анықтайды немесе (2. 4) - формуласымен есептейді:
. (2. 4)
В шкаласы (қызыл түсті ) бойынша жұмсақ аз көміртекті болаттар мен қорытпалардың қаттылығын анықтайды немесе (2. 5) -формуласымен есептейді:
. (2. 5)
Қызыл (В) шкаласы қара шкаланың бастапқы нөл белгісінен 30 бөлікке солға қарай ығысып орналасқан. Шкаланың бір бөлімінің өлшемі 0, 002 мм.
Ондағы h 0 - Р 0 бастапқы күш әсерінен пайда болатын үлгідегі тереңдік, мм.
h - Р 1 ақтық күш әсерінен пайда болатын үлгідегі тереңдік, мм.
2. 4- суреті (а, б) . Роквелл бойынша қаттылықты анықтау схемасы.
Роквелл әдісі бойынша қаттылықты өлшейтін аспаптар:
- Аспаптар ТР 5014, ТР 5014-01 (2. 5 сурет) .
Бұл аспаптар Роквелл әдісі бойынша ГОСТ 9013 бойынша металлдар мен құймалар, пластмасс, графита и электрографиттердің қаттылықтарын өлшеуге арналған. ИСО 6508, ДИН 50103 және АСТМ Е 18 аспаптарымен сәйкесінше қаттылықты өлшеуге мүмкіндік береді.
Роквеллдің 15 шкаласы бойынша қаттылықты өлшеудің кең диапазоны инденторлармен: алмаздық ұшы және диаметрлері 1, 588; 3, 175; 5; 6, 35; 10; 12, 7 мм шарлармен жүзеге асырылады.
Күшті ауыстыру тұтқаны айналдыру арқылы жүргізіледі.
Сынау орнында жарықтандырғышы бар.
ТР 5014-01 аспабы қосымша негізгі күштеменің автоматты қосымшасына және математикалық өңдеуге ие.
2. 5-сурет. Роквелл әдісі бойынша қаттылықты өлшейтін аспап ТР 5014, ТР 014-01
- Роквеллдiң әдiсi бойынша қаттылықтың өлшемдерi үшiн ТРП - 5011 аспабын қолданады (2. 6-сурет) . Роквелл бойынша қаттылықтың өлшеу ауқымының шкаласы: 70 93 HRA, 25 100 HR, 20 70 HR С. Сынау жүктемелері: алдын ала 98, 07 Н, жалпы 588, 4; 980, 7; 1471 Н. Аспаптың салмағы 7, 4 кг.
2. 6-сурет. Роквеллдiң әдiсi бойынша қаттылықты өлшеуге арналған құрал ТРП - 5011
Роквелл әдісін аз күштемеде қолданудың аумағын кеңейту үшін Супер-Роквелл әдісін қолданған дұрыс.
Супер-Роквелл әдісі бойынша қаттылықты өлшейтін аспаптар:
2143 ТРС-М аспабы (2. 7-сурет)
2. 7-сурет. Супер-Роквелл әдісі бойынша қаттылықты өлшейтін 2143 ТРС-М аспабы.
Зертханалар, металлургиялық және машина жасау кәсiпорындарының шарттары сәйкес 2143 ТРС-М аспабы Супер Роквелл әдiсі бойынша металлдар және балқымалардың қаттылығын өлшеу үшiн арналған . Аспап мыналарға сәйкес қаттылықты өлшеуге мүмкiндiк бередi: Р1024 ИСО - 1969, 50103, Е18-74 2-шi бөлiгі.
2. 1. 3 Виккерс әдісі бойынша қаттылықты анықтау
Виккерс әдісі - төртқырлы алмазды пирамиданың беткейге басылған таңбасының аумағымен анықталады. Қаттылық пирамидаға салынған күштің белгінің аумағының қатынасына тең. Виккерс бойынша қаттылық өлшем бірлігі кгс/мм². Осы әдіс бойынша анықталған қаттылық HV деп белгіленеді [2] .
Әдістің мәні зерттелетін материалға дұрыс төртқырлы алмазды пирамидамен қарама қарсы қыр арасында 136° бұрышпен басу.
Виккерс бойынша қаттылық Р жүктемені алынған пирамидалық таңба беткейінің аумағына бөлу арқылы анықталады (2. 8-сурет) . Виккерс әдісі азотталған және сегменттелген беткейлердің және жұқа парақтық материалдардың қаттылығын анықтауға мүмкіндік береді.
Виккерс пен Бринелл бойынша қаттылық мәні 100 ден 450 НВ аралығында жақсы сәйкестілік байқалады. Виккерс бойынша қаттылық барлық жағдайларда МПа (кгс/мм²) өлшем бірлігінсіз HV әріпімен белгіленеді.
Виккерс бойынша қаттылықты өлшеу кезінде негізгі параметрлер Р = 294 Н (30 кгс) жүктеме және төзімдік уақыты 10-15 с болып табылады.
Басқа жағдайларда HV белгісінен кейін қиғаш сызықпен бөлінген жүктемені және шыдамдылық уақытын білдіретін индекстер көрсетіледі және сызық арқылы қаттылық саны жазылады.
Виккерс әдісі бойынша қаттылықты өлшеу арнайы жүктеме әсерімен қыр арасындағы бұрышы 136° төртқырлы алмазды пирамидамен басуға, берілген уақыт аралығында салынған жүктеме тұрақтылығын ұстап тұруға және жүктемені алғаннан кейінгі қалған таңбаның (белгінің) диагоналін өлшеуге негізделген. Белгі орталарының ара қашықтығы мен көрші белгінің шетіне дейінгі қашықтығы белгінің диоганалінің 2, 5 ұзындығынан кем болмауы керек.
Виккерс бойынша қаттылық мына формуламен (2. 6) анықталады:
Егер Р жүктемесі кгс-да анықталса,
, (2. 6)
Мұндағы, α - пирамида шыңынан алғанда қарама-қарсы қабырғаларының арасындағы бұрыш.
2. 8-сурет. Виккерс бойынша қаттылықты анықтау схемасы.
Виккерс әдісі бойынша қаттылықты өлшейтін аспаптар:
- Металлдар мен құймалар қаттылығын өлшейтін әмбебап аспаптар ИТ 5010, ИТ 5010-01М (2. 9 сурет) .
Аспаптар Виккерс және Бринелл әдісі бойынша металлдар мен құймалардың қаттылығын өлшеуге арналған.
2. 9- сурет. Металлдар мен құймалар қаттылығын өлшейтін әмбебап аспап ИТ 5010-01М.
ИТ 5010 аспабы- электронды санау жүйесі жоқ. ИТ 5010-01М аспабы- электронды санау жүйесімен.
Электронды санау жүйесі шығаруға мүмкіндік береді:
- бұйымды қаттылық тобына: АЗ, ҚАЛЫПТЫ, ҮЛКЕН;
- өлшеу қорытындысының математикалық өңдеуін;
- топтамадағы жоғары және төменгі мағынаны табу;
- топтамадағы орташа мағынаны табу;
- көрсеткіштердің қарқынын анықтау.
Сандық табло өлшем қорытындысын санау үшін және керекті берілгендерді енгізуде көзбен көру үшін қызмет етеді. Аспап ЭЕМ-ға шығуға және басып шығуға қабілетті [5, 6] .
- Портативті аспап ИТ 5160 (2. 10-сурет) .
Зертханалық, цехтық және алаң жағдайларында жазық және қисықсызықты беткейлерде болат өнімдері мен оның құймаларының қаттылығын өлшеуге арналған аспап.
Аспап - датчиктен, электрондық блоктан және біріктіргіш құрылымнан тұратын қоректендіру блогынан тұрады.
Аспапта қөзге көрінетін қаттылықтың үш тобы бар: ТӨМЕН-ҚАЛЫПТЫ-ЖОҒАРЫ жарықтық және дыбыстық сигналмен.
Аспаптың қоректенуі - автономды (8 сағаттан аз емес, аккумуляторлар)
және 220 В ауыспалы тоқ күштемесі желісінен.
2. 10-сурет. Виккерс бойынша металлдың қаттылығын өлшеу үшін портативті аспап ИТ 5160
Бринеллдің әдiсімен салыстырғанда, Виккерс әдiсiнiң артықшылығы - Виккерстiң әдiсiмен алмас пирамиданы қолдану барысында материалдардың жоғары қаттылықты сынауға болатындығында.
2. 2 Динамикалық әдіс бойынша қаттылықты анықтау
2. 2. 1 Шора бойынша қаттылық
... жалғасы- Іс жүргізу
- Автоматтандыру, Техника
- Алғашқы әскери дайындық
- Астрономия
- Ауыл шаруашылығы
- Банк ісі
- Бизнесті бағалау
- Биология
- Бухгалтерлік іс
- Валеология
- Ветеринария
- География
- Геология, Геофизика, Геодезия
- Дін
- Ет, сүт, шарап өнімдері
- Жалпы тарих
- Жер кадастрі, Жылжымайтын мүлік
- Журналистика
- Информатика
- Кеден ісі
- Маркетинг
- Математика, Геометрия
- Медицина
- Мемлекеттік басқару
- Менеджмент
- Мұнай, Газ
- Мұрағат ісі
- Мәдениеттану
- ОБЖ (Основы безопасности жизнедеятельности)
- Педагогика
- Полиграфия
- Психология
- Салық
- Саясаттану
- Сақтандыру
- Сертификаттау, стандарттау
- Социология, Демография
- Спорт
- Статистика
- Тілтану, Филология
- Тарихи тұлғалар
- Тау-кен ісі
- Транспорт
- Туризм
- Физика
- Философия
- Халықаралық қатынастар
- Химия
- Экология, Қоршаған ортаны қорғау
- Экономика
- Экономикалық география
- Электротехника
- Қазақстан тарихы
- Қаржы
- Құрылыс
- Құқық, Криминалистика
- Әдебиет
- Өнер, музыка
- Өнеркәсіп, Өндіріс
Қазақ тілінде жазылған рефераттар, курстық жұмыстар, дипломдық жұмыстар бойынша біздің қор #1 болып табылады.

Ақпарат
Қосымша
Email: info@stud.kz