Машина жасау жайлы


Жұмыс түрі: Дипломдық жұмыс
Тегін: Антиплагиат
Көлемі: 76 бет
Таңдаулыға:
КІРІСПЕ . . . 7
1ТЕХНОЛОГИЯЛЫҚ БӨЛІМ . . . 10
- Бұйымның қызметтік тағайындалғандығы жөнінде мәліметтер құрылымы . . . 10
1. 2 Бөлшекті технологиялық тұрғыдан талдау . . . 12
1. 3 Өндіріс түрін анықтау . . . 16
1. 4 Дайындама алу әдістерін таңдап негіздеу . . . 17
1. 5 Бөлшекті жасауда технологиялық базаларды таңдау . . . 23
1. 6 Бөлшекті өңдеудің маршруттық технологиясын таңдау . . . 23
1. 7 Әдіптерді есептеу . . . 25
1. 8 Кесу режимдерін есептеу . . . 30
1. 9 Техникалық уақыт нормасын есептеу . . . 35
2. КОНСТРУКТОРЛЫҚ БӨЛІМ . . . 40
2. 1 Айлабұйым таңдау мен оны жобалау . . . 40 2. 2 Кескіш аспапты таңдау және есептеу . . . 40
3. ҰЙЫМДАСТЫРУ БӨЛІМІ . . . 47
3. 1 Білдекті немесе өңдеу жабдығын таңдау . . . 47
3. 2 Өндірістің негізгі жабдықтар санын анықтау . . . 49
3. 3 Цех жұмысшыларының саны мен құрамын анықтау . . . 51
3. 4 Механикалық бөлімнің ауданын анықтау . . . 51
3. 5Механикалық бөлімнің көмекші бөлімнің ауданын есептеу . . . 52
3. 6 Материалдар мен дайындамаларды сақтайтын қойманың ауданын
есептеу . . . 52
3. 7 Құрастыру стендінің санын анықтау . . . 52
3. 8 Құрал-жабдық қоймасының ауданын анықтау . . . 53
3. 9 Құрастыру бөлімінің ауданын анықтау . . . 53
3. 10 Механикалық құрастыру бөліміндегі жұмысшылар санын
анықтау . . . 53
3. 11 Қызмет көрсету мекемесін жобалау . . . 54
4 ЕҢБЕКТІ ҚОРҒАУ ЖӘНЕ ТЕХНИКА ҚАУІПСІЗДІГІ . . . 56
4. 1 Еңбекті қорғау шараларын ұйымдастыру . . . 56
4. 2 Қауіпсіз еңбек жағдайларын қамтамасыз етудің кешенді
іс-шаралары . . . 56
4. 3 Еңбек қауіпсіздігінің техникалық шаралары . . . 58
4. 4 Технологиялық жабдық пен негізгі өндірістік процестің қауіпсіздігін
қамтамасыз ету . . . 59
4. 5 Материалдарды кесу аспаптары мен механикалық өңдеудегі
қауіпсіздік ережелері . . . 61
4. 6 Жерге қосылғыш қондырғыны есептеу . . . 62
4. 7 Шу мен діріл деңгейін есептеу . . . 66
4. 8 Жасанды жарықтандыруды есептеу . . . 67
4. 9 Өрт қауіпсіздік шаралары . . . 68
4. 10Еңбек пен демалу режимдері . . . 70
4. 11 Микроклиматты қамтамасыз ету . . . 70
4. 12 Жарақаттану мен кәсіби аурудың пайда болуына себепші
факторлар . . . 71
5 ЭКОНОМИКАЛЫҚ БӨЛІМ . . . 73
5. 1 Негізгі өндірістік қорды есептеу . . . 73
5. 2 Негізгі өндірістік қордың басқа элементтерін есептеу . . . 74
5. 3Өнеркәсіп жұмысшыларының санын есептеу . . . 76
5. 4 Материалдың, энергияның, аспаптың және тетіктің шығындарын
есептеу . . . 77
5. 5 Жалақы қорын есептеу . . . 80
5. 6 Шығындардың статьялары . . . 83
5. 7Цехтардың шығындарын есептеу . . . 85
5. 8Өнімнің өзіндік құны . . . 86
5. 9 Айналым қаражаттарын есептеу . . . 88
5. 10 Жобалап отырған цехтың, учаскенің техникалық-эканомикалық
көрсеткіштері . . . 88
ҚОРЫТЫНДЫ . . . 91
ҚОЛДАНЫЛҒАН ӘДЕБИЕТТЕР ТІЗІМІ . . . 92
КІРІСПЕ
Өндірістің тиімділігі, оның техникалық прогресі, шығарылатын өнімнін, сапасы көбінесе жаңа жабдықтарды, машиналарды, станоктар мен аппараттарды шығаруға, сондай-ақ технологиялық және конструкторлық шешімдердің экономикалық тиімділігі мен техникалық мәселелерді қамтамасыз ететін әдістерді жан-жақты енгізуге байланысты. Ғылыми-техникалық революцияны жүзеге асыруда машина жасау саласы басты, өзекті роль атқарады. Оның өсу қарқынын XII бесжылдықтың өзінде-ақ бір жарым-екі есе арттыру көзделіп отыр.
Қолда бар қуатты мейлінше толык пайдалану және саланың ең бірінші кезекте қайта құрылуын жүзеге асыру міндеті алға қойылады. Бұл үшін қайта бөлу есебінен машина жасауға жұмсалатын күрделі қаржыны 1, 8-2 есе ұлғайтып, қазіргі заманға сай жабдық түрлерін беруді шұғыл арттырған жөн.
Өндірістік процестерді жобалаудың инженерлік әдістерін толықтай игере алатын маман кадрларды даярлауда осы мәселелердің бәрін жолға қоюдың маңыздылығы зор.
Бүгінгі заман талабы ғылыми - техникалықпрогресті және әлеуметтік міндеттердің ойдағыдай шешілуін қамтамасыз ететін салаларды неғұрлым жоғары қарқынмен дамыту, тұтыну мен қор жинаудың оңтайлы арақатынасына, өндіріс құрал- жабдықтары мен тұтыну заттарын өндіруге аграрлық- өнеркәсіптік кешеннің салалары арасындағы пропорцияларды жақсы артуға күш салуды қажет етеді.
Еліміздің экономикасын дүние жүзіндегі ең жетілдірілген және қуатты экономикаға айналдыру экономикалық күш- қуаттың негізі- ауыр индустрияны одан әрі дамытуды қажет етеді.
Ғылым мен техниканың ең жаңа жетістіктерін іске қосуда машинажасау саласына басты орын берген жөн. Оның өсу қарқынын жеделдету- халық шаруашылығының барлық салаларындағы ғылыми- техникалық прогрестің және елдің қорғаныс қабілетін тиісті дәрежеде ұстаудың негізі, болашақта экономиканы дамытудың сара бағыты. Машинажасау өндірісінің технологиясы мен ұйымдастырылуында революциялық өзгерістер жасауды, еңбек өнімділігін еселеп арттыруды, материал мен энергияның жұмсалуын кемітуді, өнімнің сапасын жақсыартуды, қор қайтарымын өсіруді қамтамасыз ететін техникалық- экономикалық жағынан ең жоғары дәрежедегі машиналар, жабдықтар мен аспаптар жүйелері мен комплектілерін шығаруға тиіс. Ғылыми- техникалық прогресті жеделдетудің шын мәніндегі тездеткіштері - станок жасау, электротехника өнеркәсібі, микроэлектроника, есептеу техникасы мен прибор жасау, бүкіл информатика индустриясы басым дамытылатын болады.
Қазіргі еліміздің бетбұрыс дәуіріндегі ғылыми- техникалық прогрестің басым бағыттарының алдына қойған негізгі мәселелері мейлінше жаңа технологиялық процестер мен операциялар ашу және халық шаруашылығындағы осы уақытқа дейін ашылған, пайдаланып келе жатқан технологиялық процестер мен операцияларды ұтымды қолдану болып отыр.
Бұл мәселенің көкейтесті мақсаттары мынадай:
- елімізде шығаратын өндірістік бұйымдардың сапасын дүние жүзінде шығарылатын бұйымдардың сапасынан арттыру немесе соларға пара- пар етіп шығару;
- бұйымдарды шығаратын өндірістің экологиялық тазалықты сақтау және өндірістің қауіпсіз жағдайда қызмет етуі;
- өндірісті барынша ынталандырып, жоғары сапалы өнімдер алу;
- бағдарламамен басқарылатын станоктарды пайдалану;
- бұйымдар шығаратын өндірістің ресурс сыйымдылығын, шығынын (еңбекке, материалдарға, энергияға, негізгі қорларға, өндіріске жұмсалған қаржыға кететін және т. б. ) азайту.
Осы мақсатта машинажасау салаларының өте маңызды бағыттары төмендегідей деген пікір айтуға болады:
- машинажасау кешенін, ең алдымен станок жасауды, есептеу техникасы өндірісін, прибор жасауды, электротехника және электрон өнеркәсібін түпкілікті қайта құрып, озық дамыту;
- машинажасау кешенін дамытуға жұмсалатын күрделі қаржының көлемін едәуір арттыру;
- жаңа техника жасау мен игеру мерзімін қысқартудың көптеген техникалық және экономикалық мәселелерін шешу;
- қайта реттелетін икемді өндірістер мен автоматтандырылған жобалау жүйелері, автомат желілері, микропроцессорлық техника құралдары орнатылған машиналар мен жабдықтар, сандық бағдарламамен басқарылатын көп операциялы станоктар робот- техникалық, роторлы және роторлы-конвейерлі кешендердің кеңінен енгізілуіне жол ашу;
- тораптар мен бәлшектерді барынша бірыңғайлауға күш салу;
- бірыңғайланған блоктық- модульдік және базалық конструкциялар негізінде машиналар, жабдықтар мен приборлар жасау жөніндегі шараларды жүзеге асыру;
Сандық бағдарламамен басқарылатын металл жонатын станоктарды, «өңдеу ортадағы» үлгісіндегі станоктарды, ауыр және бірегей станоктар мен престерді, машинажасау саласында жаппай шығарылатын өнімдерді құрастыруды автоматтандыруға арналған жабдықты, роторлы, роторлы- конвейрлі және машинажасау мен металл өңдеуге арналған басқа да автоматты линияларды озық қарқынмен шығаруды қамтамасыз ету қажет. Дәлдігі жоғары және аса жоғары станоктар шығару елеулі түрде кеңейтілуі шарт.
Автоматтандырылған және роботтандырылған кешендер мен линиялар, металл өңдеудің икемді өндірістік жүйелерін, оның ішінде табақшалап және аумақтап штамптауға, металл ұнтақтарынан, пластмассалардан және басқа металдардан бөлшектер, прогресті аспап пен технологиялық жабдық, бақылауды автоматтандырудың осы заманғы өлшеу құралдарын өндіруге арналған жүйелерді жасаудың ұлғайтылуы көзделгені жөн.
Қысқасы, Қазақстандық машина жасау саласын өрге бастыру міндеті - бұл біздің дамуымыздың сара бағыты, сондықтан оны қазір де, келешекге де берік ұстану қажет.
1. ТЕХНОЛОГИЯЛЫҚ БӨЛІМ
1. 1 Бұйымның қызметтік тағайындалғандығы жөнінде мәліметтер құрылымы
9Д 100. 37. 141 Біріктіруші білігі редукторлы ауаүрлегішті редуктор приводыемен жалғастырып тұруға негізделген. Негізгі қызметі айналу моментін сол қалпында өзгертпестен бір бөлітен екінші жалғастырушы бөлігіне беру.
1-сурет. Редукторлы ауаүрлегіштің сұлбасы
1. валик
2. шпилька
3. шайба
4. вал соединительный
6. шайба стопорная
7. пружина
8. валик
9. шпилька
10. втулка
11. муфта
12. шестерня
13. корпус редуктора
14. болт
15. крышка
16. прокладка
17. крышка редуктора
18. прокладка
20. болт сухаря
21. муфта переходная
22. сухарь
23. пружина
24. ступица
25. диск
26. втулка
27. втулка
30. фланец нажимной
33. маслоуловитель
34. гайка
35. болт
37. шайба замковая
38. гайка
39. кольцо стопорное
40. кольцо уплотнительное
41. втулка
43. планка стопорная
44. прокладка
49. кольцо уплотнительное
50. диффузор лопаточный
52. прокладка
54. прокладка
55. крышка
56. шайба замковая
58. гайка
59. болт
60. гайка
61. болт
62. кольцо
63. кольцо проставочное
64. кольцо уплотнительное
65. кольцо упорное
66. фланец
67. прокладка
68. втулка
70. отбойник
74. подшипник опорный
75. вал
76. подшипник упорно-опорный
77. вал промежуточный
78. гайка
79. втулка
80. подшипник
81. шпилька
82. пита
83. гайка
84. болт
85. гайка
86. болт
89. фланец нажимной
1. 2 Бөлшекті технологиялық тұрғыдан талдау
Біліктің конструкциясының лайықтылығын зерттеу .
Бұйым құрылымының оның өндіру технологиясымен байланысты әзірленген өндірістің технологиялық әзірлігінің күрделі функцияларының бірі - бұйым құрылымының технологиялық лайықтылығымен қамтамасыз ету. Бұл қызмет дәл және толық орындалмаса өндірістік негізсіз еңбек шығындары, материал, құрал, уақыт шығындары күрт жоғарлайды. Құрылымдардың технологиялық лайықтылығын тексеру бұйым шығарудың әрбір кезеңінде ӨТӘБЖ (ЕСТПП) стандарттары орнатылады. Машина құрылымының жетілгендігі қазіргі техниканың даму деңгейіне сәйкестігімен, тиімділігімен, пайдалану қолайлылығы-мен және алынған өндіріс жағдайында өнімді техникалық әдістерді тиімді пайдалану мүмкіндңктері деңгейін ескеілгендігімен мінезделеді. Машина құрылы-мының осы мүмкіндіктерінің толық ескерілуі, оның техникалық лайықтылығын көрсетеді. Бұйым құрылымының техникалық лайықтылығы дегеніміз оның өндіру кезінде болатын шығындарды ұтымды шектеуге пайдалану және жөндеудегі шығындарды шығару көлеміне қызметті орындау жағдайлары берілген сапа көрсеткішіне сай етуге мінезделгендігін анықтайтын қасиеттер жинағы. Осыған байланысты техникалық лайықтылық салыстырмалы түсінік. Бір бұйымның техникалық лайықтылығы әртүрлі өндіріс түріне, нақты өндіріс жағдайына байланысты әртүрлі болуы мүмкін, сонымен қатар техникалық лайықтылық кешенді түсінік, оны бөлек дайындама үрдістерінсіз өңдеу, жинау, бақылау, пайдалану және жөндеу үрдістерін ескермей қарауға болмайды.
Техникалық лайықтылық көрсеткіштерін жақсартып, өндіріс құралдарын өзгертпей өнім шығару деңгейін жоғарлатуға болады. Бұйымның техникалық лайықтылығын қамтамасыз етудің негізгі мақсаты еңбек, материал, отын, қуат шығындарын ұтымды жобалау, өндірісті дайындау, өндіріс техникалығы және техникалық күту, жөндеу кезеңдерінде бұйым сапасын өз алдына қамтамасыз етіп, алынған өндіріс жағдайына жету. Бұйымның төрт түрін жіктеуге болады: деталь, жинақ бірлігі, кешен, жинақ. Өндіріс келесі үш түрге бөлінеді: жеке, сериялы, жаппай мол.
Технологиялық лайықтылық түрлері бұйым конструкциясының технологиялық лайықтылық қасиеттері бейнеленетін салаларды мінездейді. Бұл салалар:
- өндірістік;
- пайдалану;
-жөндеу.
Өндірістік техникалық лайықтылық келесі бағыттарда материал және уақыт шығындарын қысқартумен белгіленеді:
-өндірістің конструкциясын дайындау;
- өндірістің техникасын дайындау;
-жасау үрдістері.
Пайдалану техникалық лайықтылық қаржы және уақыт шығындарын
-техникалық және технологиялық күтуге;
- ағынды және толық жөндеуге;
-жөндеу техникалық лайықтылығы.
жөндеудің барлық түрлерге кететін шығындарын қысқартуды
қарастырады.
1. 1 - кесте
Тетікті лайықтылыққа зерттеу.
Бұйымның технологиялық лайықтылығын есептеудің сапалы бағасын келесі көрсеткіштерден аламыз.
1. Құрылымдық элементтің унификациялау коэффициентін анықтаймыз:
(1. 1)
Мұнда К уэ - құрылымдық элементтерінің унификациялау коэффициенті;
Q уэ - құрылымдық элементтердің унификацияланған түр мөлшерінің (бұрандалар, тесіктер, тығырықтар, фаскалар, т. б. ) саны;
Q э - бұйымдағы құрылымдық элементтердің жалпы саны;
![]()
ЕСТПП бойынша К уэ = 0, 65 жоғары болуы керек.
2. Өңдеу дәлдігінің коэффициентін анықтаймыз:
(1. 2)
(1. 3)
Мұнда А ср - өңдеу дәлдігінің орташа квалитеті;
А - өңдеу дәлдігінің квалитеті;
n 1 - квалитетке сай мөлшерлер саны;
Неғұрлым К ТО үлкен болса, соғұрлым конструкция лайықтырақ болады.
К ТО = 0, 92 > 0, 5 бұйым орташа дәлдікті.
3. Кедір бұдырлық коэффициенті келесіше анықталады:
Б
ср
(1. 4)
Мұнда Б ср - келтіру коэффициентінің орташа шамасы;
Б - келтіру коэффициентінің шамасы;
n nш - кедір-бұдырлық параметрінің лайықты беттер саны.
К
ш
(1. 5)
0, 25 < 0, 16 Бұл көрсеткіш бойынша да бұйым орташа дәлдіктілер қатарына жатады. Табылған мәліметтер төменгі кестелерге енгізіледі.
1. 2-кесте.
Деталь құрылымының технологиялық лайықтылық көрсеткіштерін бағалау.

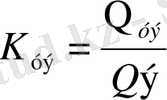

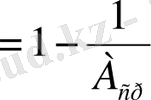

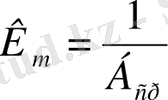
Детальдың технологиялық лайықтылығын сараптау қорытындысында келесі жағдайлар анықталған:
- бұйым орташа дәлдікті қатарына жатады.
-құрылымның технологиялық лайықтылығының сандық бағалау коэффициентіне сәйкес бұйым технологиялық лайықты болып есептеледі.
1. 3 Өндіріс түрін анықтау
Өндірістік бағдарлама мөлшеріне, өнімнің сипатына, сондай-ақ өндірістік процесті жүзеге асырудың технологиялық және экономикалық шарттарына байланысты барлық сан алуан өндірістер үш негізгі түрге: жеке; сериялық; көптік өндіріс болып бөлінеді.
Өндіріс түрін анықтау МЕСТ 3. 1108-74 стандартымен операцияны
бекіту коэффициетімен сипатталады:
K о. б =Q/P м (1. 6)
Мұндағы: Q - әр түрлі операциялардың саны;
P о - орындалатын операциялардың жұмыс орны саны.
Өндіріс түрі келесідей операцияларды бекіту коэффициеттермен анықталады.
1. 3 - кесте.
Операцияларды бекіту коэффициентіне байланысты өндіріс түрі.
Көптік
Сериялық:
ірі сериялық
орташа сериялық
уақ сериялық
Жеке
<1
1-10
10-20
20-40
40<
Тіректе технологиялық процесінде операциялар саны: Q= 15.
Орындалатын операциялардың жұмыс орны саны: P о = 3.
K о. б =15/3= 5
Анықталған мән бойынша 1. 1 - ші кестеден өндіріс түрі:
сериялық, оның ішінде ірі сериялық.
1. 4 - кесте.
Бұйым массасы мен өндіріс түріне байланысты жылдық шығару көлемі (дана)
Бұйым
салмағы,
кг
Уақ
сериялы
Орташа
сериялы
Ірі
сериялы
10 3
Көптік
10 3
<1, 0
1, 0-2, 5
2, 5-5, 0
5, 0-10
>10
<10
<10
<10
<10
<10
10-2000
10-1000
10-500
10-300
10-200
1500-1
1000-5
500-35000
300-25000
200-1
75-200
50-100
35-75
25-50
10-25
200
100
75
50
25
Келесі параметр - жылдық шығару көлемін 1. 2 - ші кестесінен анықтаймыз.
Жылдық шығару көлемі - 1 дана етіп қабылдаймыз.
1. 4 Дайындама алу әдістерін таңдап негіздеу
Машинажасау саласында дайындама деп - кезекті өңдеу арқылы әзір бұйым жасауға арналған жартылай фабрикатты (илеме, соқпа, құйма, т. б. ) атайды.
Дайындаманы таңдау бұйым жасау процестерін жобалаудағы ең маңызды мәселелердің бірі болып саналады. Оның дұрыс таңдалғанына операциялар немесе ауысулар саны, еңбек сыйымдылығы, ақыр соңында жалпы бұйымды жасау өзіндік құнына байланысты болады. Дайындаманы алудың таңдалған әдісі бұдан әрі болатын өңдеу процесін айқындайды. Егер дайындаманы жасау дәлдігі біршама жоғары болса, бұйымның механикалық өңдеуі ең аз операцияларды талап етіп, еңбек сыйымдылығы мен құнын төмендетеді.
Дайындама тұрпайы жасалған болса бұйымды өңдеу процесі қымбатсиды. Сол себепті дайындаманы таңдағанда неғұрлым әзір бұйымға жақын өлшемдерін, салмағын, конструкциясын және т. б. параметрлерін ескеру қажет.
Дайындама алудың техника-экономикалық есептері келесідей екі нұсқа бойынша жүргізіледі: сортты илеме және ыссылай штамптау. Жылдық бағдарлама бойынша 1 дана. Бөлшек массасы 6, 77 кг. Материал: Болат45ХН2МФА Өндіріс типі-ірі сериялы.
1-Нұсқа.
Есептік негізде дайындама алу үшін МЕСТ 7417-75 бойынша қарапайым дәлдәкте қажетті өлшемдегі сортты прокат аламыз.
Берілген диаметр бойынша нормальды ұзындық 4 . . . 7 м болып табылады.
Дайындаманың толық ұзындығын есептейміз.
L д - бөлшектің ұзындығы
Z подр - бүйір бетін өңдеуге қалдырылған әдіп
Дайындаманың көлемін есептейміз
,
L З - дайындаманың ұзындығы, см;
D З. П - дайындаманың диаметр, см.
Дайындаманың массасын есептейміз:
γ- материалдың тығыздығы.
;
Дайындаманың қысуға кеткен өлшемі l ЗАЖ. =80 мм.
Дайындаманың бүйірін кесуге кететін өлшемі:
d - дайындама диаметрі,
d=75 мм.
Дайындаманың санын келесі формула бойынша есептейміз:
,
L ПР - қабылданғанилеменің ұзындығы.
Илеменің ұзындығы 4 м болған кезде:
6 дайындама аламыз.
Илеменің ұзындығы 7 м болған кезде:
11 дайындама аламыз.
Қабылданған өлшемі бойынша қалдық ұзындықты есептейміз.
немесе
;
Илеменің ұзындығы4 м. :
немесе
Илеменің ұзындығы7 м. :
немесе
Бұл есептің қорытындысы бойынша 7 м илеме 4 м илемеге қарағанды тиімді.
Қысуға кеткен материалдың кесу кезіндегі илеменің ұзындығына қатынасы келесідей есептеледі:
;
Бүйілік кесудегі илеменің кеткен ұзындығынығ илеменің ұзындығына проценттік қатынасы кеесідей есептеледі:
;
Қабылдаған илеменің ұзындығына кеткен жалпы шығын:
;
Барлық технологиялық қалдықтарды қосқандағы бір бөлшекке кететін материал шығыны:
;
Материалды қолданукоэффициенті:
;
Илемеден жасалған дайындама құны келесі формула бойынша есептеледі:
(1. 7)
Мұндағы,
- 1 кг дайындама материалының құны, теңге;
- илемеден алынған дайындама массасы, кг;
q - әзір бұйымның салмағы, кг;
- 1 тонна қалдықтың бағасы, теңге;
Сонда:
тг
Екінші жағдайда:
Дайындама ыссылай көлемдік штамптау әдісі бойынша горизонтальды соғу машинасымен (ГСМ) алынған
Қыздыру әдісі: индукциялық
Соқпаны жасау дәлдігі - Т4
Күрделілік дәрежесі - С1.
Болат тобы - М1 [1- кесте, 3]
Қалып аралықтар- жазықтық П [1- кесте, 3]
Бастапқы индекс- 15 [11- кесте, 3]
Соқпа салмағын есептеу үшін деталь салмағын есепті коэффициентке
көбейтеміз: Әдістемелік ңұсқаудан [2-кесте, 3]
G д = 6, 77×1, 45=9, 8 кг
d=66. 8×1. 05=70. 14мм.
ℓ=565×1, 05=593, 25
Әдіптер мен ұсталық артық шығулар.
Мөлшерлерге негізгі әдіптерді беру [12- кесте, 3]
1, 8 - диаметр 82 мм және бет тазалығы 3, 2;
1, 6 - диаметр 42 мм және бет тазалығы 1, 6;
1, 7 - радиус 100мм және бет тазалығы 1, 6;
2, 6 - қалыңдық 565 мм және бет тазалығы 12, 5
Жазықтықтан ауытқуды ескеретін қосымша әдіп- 1 мм. [4- кесте, 3]
Соқпаның мөлшерлері:
Қабылданған:
Диаметр 66, 8+(1, 8+1) ×2= 71, 6 72
Диаметр 42+(1, 6+0, 6) ×2=46, 4 47
Радиус 100+(1, 7+0, 6) ×2=104, 6 105
Қалыңдық 565+(2, 6+0, 6) ×2=571, 4 572
Сыртқы бұрыштарының шеңберлену радиусы- 2, 0мм.
Мөлшерлердің шекті ауытқулары [13-кесте, 3]
Диаметрі
Диаметрі
Радиус
Қалыңдығы
Соғылған және штампталған дайындамалардың бағасы келесі формуламен анықталады:
(1. 8)
Мұндағы:
- 1 кг соқпа немесе штампталған дайындаманың құны, теңге;
соқпа массасы, кг;
q - әзір бұйымның салмағы, кг;
- 1 тонна қалдықтың құны, теңге;
1 кг соқпаның бағасы соқпалардың 1 тоннасының нормативтік өзіндік құны мен белгілі жағдайларға лайықты элемент- коффициент арқылы анықталады:
(1. 9)
Мұнда,
- анықталған шарт бойынша 1 тонна соқпаның нормалық өзіндік құны, тоннаға теңге;
- соқпа дәлдігіне тәуелді түзету коэффициенті;
- соқпаның күрделілік тобына тәуелді түзету коэффициенті;
- соқпаның массасына тәуелді түзету коэффициенті;
- соқпа материалының маркасына тәуелді түзету коэффициенті;
- өндіріс көлеміне тәуелді түзету коэффициенті.
тг/т
Олай болса:
тг
Штамптау әдісін қолданғанда шартты үнемдеу жылына:
Э= (С Д1 - С Д2 ) ×N= (9491-8616) ×1=875тг
Материалдың жылдық үнемделуі:
(Q 2 - Q 1 ) ×N= (21, 5- 17, 9) ×1= 36000 кг
Негізгі технологиялық процесте- бастапқы дайындама домалақ тәрізді илеме алынған. Оның салмағы- 21, 5 кг тең.
Ал жобаланған технологиялық процесте- бастапқы дайындама ретінде бұйым пішініне сәйкес пресс қалыпта штампталған дайындама аламыз. Өндіріс түрі- сериялық және жылдық шығару бағдарламамыз 1 дана болғандықтан дайындаманы пресс қалыпта штамптаған тиімді. Сериялы өндірісте пресс қалыптарда дайындама алу кеңінен қолданылады. Алынған дайындама салмағы- 17, 9 кг. Және де таңдалған дайындама дайын бұйым пішініне жақын болғандықтан, бұрынғы технологиялық процесте жобаланған кейбір операциялар саны қысқарады. Осыған байланысты уақытты да үнемдейміз, жұмысшы саны да қысқарады. Металды, уақытты үнемдеу және де өлшемі дәл бұйым алу машинажасау өндірісінің басты мақсаты болып табылады.
1. 5 Бөлшекті жасауда технологиялық базаларды таңдау
База ретінде бөлшектің түйінге немесе станокка орнату, өлшеу үшін
... жалғасы- Іс жүргізу
- Автоматтандыру, Техника
- Алғашқы әскери дайындық
- Астрономия
- Ауыл шаруашылығы
- Банк ісі
- Бизнесті бағалау
- Биология
- Бухгалтерлік іс
- Валеология
- Ветеринария
- География
- Геология, Геофизика, Геодезия
- Дін
- Ет, сүт, шарап өнімдері
- Жалпы тарих
- Жер кадастрі, Жылжымайтын мүлік
- Журналистика
- Информатика
- Кеден ісі
- Маркетинг
- Математика, Геометрия
- Медицина
- Мемлекеттік басқару
- Менеджмент
- Мұнай, Газ
- Мұрағат ісі
- Мәдениеттану
- ОБЖ (Основы безопасности жизнедеятельности)
- Педагогика
- Полиграфия
- Психология
- Салық
- Саясаттану
- Сақтандыру
- Сертификаттау, стандарттау
- Социология, Демография
- Спорт
- Статистика
- Тілтану, Филология
- Тарихи тұлғалар
- Тау-кен ісі
- Транспорт
- Туризм
- Физика
- Философия
- Халықаралық қатынастар
- Химия
- Экология, Қоршаған ортаны қорғау
- Экономика
- Экономикалық география
- Электротехника
- Қазақстан тарихы
- Қаржы
- Құрылыс
- Құқық, Криминалистика
- Әдебиет
- Өнер, музыка
- Өнеркәсіп, Өндіріс
Қазақ тілінде жазылған рефераттар, курстық жұмыстар, дипломдық жұмыстар бойынша біздің қор #1 болып табылады.

Ақпарат
Қосымша
Email: info@stud.kz