Қатты денелерді сынау әдістері


Мазмұны
ТҮЛЕКТІК ЖҰМЫС1
Мазмұны2
Кіріспе3
І. Полимерлердің механикалық қасиеттері және оның ерекшеліктері. 5
1. 1. Қатты денелердің нақты беріктігі. 5
1. 3. Қатты денелерді сынау әдістері. 9
1. 3. 1. Созу деформациясы. 9
1. 3. 2. Сығу деформациясы17
1. 3. 3. Иілу деформациясы23
1. 3. 4. Ығысу28
1. 4. Полимерлердің қаттылығын анықтау32
1. 4. 1. Шарикті батыру арқылы қаттылықты анықтау32
1. 4. 2. Роквелль бойынша қаттылық37
1. 4. 3. Қаттылықты сүйір индентормен анықтау39
ІІ. Полимерлердің механикалық қасиеттерін зерттеу. 44
2. 1. Эксперимент әдістемесі және эксперименттік құрылғы. 44
2. 1. 1. Р-50 үзгіш машинасының құрылысы және сипаттамасы44
2. 1. 2. Материалдарының механикалық қасиеттерін анықтауға арналған құрылғы. 48
2. 2. Сынау шартын таңдау. 57
2. 3. Әртүрлі полимерлердің механикалық қасиетін зерттеу. 59
Қорытынды66
Қолданылған әдебиеттер67
Кіріспе
Полимерлердің механикалық сипаттамасы олардың қолданылу аймақтарының эксплуатациялық көрсетулерінің бірі болып саналады. Сондықтан осы материалдармен жұмыс істейтін маман, оның механикалық қасиеттерін және полимерлердің құрылыстық сипаттамасына әсер етуін білуі керек. Барлық белгілі материалдардың қасиеттерімен өте кең диапазонмен беріледі.
Өз сипаттамалары мен олар тұтқыр сұйықтар және эластомерлермен қатқыл қатты денелерге дейін өзгереді. Құрылымдық параметрлердің механикалық қасиеттерінің өзгешелігімен анықталады. Полимерлердің механикалық қасиеттеріне осы аталған құрылымдық параметрлерден басқа ішкі факторлар да үлкен ықпал етеді. Мысалы, температура, ұзақтық, жиілік, жүктеу жылдамдығы, қысым, кернеу, амплитудасы және деформациялар, кернеулік күйінің түрі, жылу өңдеулік, термиялық заңдылық, қоршаған ортаның табиғаты.
Басқа материалмен, мысалы: металдармен салыстырғанда полимерге сипаттамалы механикалық қсиет өте тез мазмұнды температуралық - уақыттық тәуелділік. Бұл тәуелділік параметрлердің деформациясының тұтқыр серпімділік табиғатымен байланысты. Барлық жұмыс тұтқыр сұйықтықта, оның деформирленгендегі көбейтіндісі жылу түрінде таралады, сол уақытта ол серпімді денеде созылған пружина сияқты потенциялық энергия түрінде жабысады. Полимерлердің бұл табиғаты олардың механикалық қасиетін қиындатады және сол уақытта теориялық жағынан қызықты.
Полимерлердің мінездемесін анықтайтын көптеген белгілі әдістер механикалық сынақтар мен факторлар, олардың механикалық қасиетін өте қиын етіп жасар еді, егер де бірнеше жалпы құбылыс және эмпирикалық ереже, көптеген сұрақтардың шешімін қысқартпаған кезде.
І. Полимерлердің механикалық қасиеттері және оның ерекшеліктері.
1. 1. Қатты денелердің нақты беріктігі.
Техникалық беріктік дегеніміз - техникада қолданылып жүрген қатты денелер мен полимерлердің нақты беріктігі. Теориялық және техникалық беріктік қатынастары берілген кестеде теориялық беріктік техникалық беріктіктен 100-1000 есе артық көрсетілген. Нақты денелердегі ақаулар оның беріктігін кемітеді. Техникалық беріктіктің есептеу әдістерін алғаш рет ағылшын физигі Гриффитс ашқан еді. Ол әдістің мәні мынадай: жұқа пластина түріндегі үлгіге кернеу түсіріледі. Осындағы серпімді энергия тығыздығы -
Үлгі
кернеу әсерінен деформацияланады:
![]()
Абсалют деформация
үлгі ұзындығы.
Үлгі ұзарғандағы кернеудің істейтін жұмысы
(1. 1. )
Бұл жұмыс көлемі V болатын үлгіні серпімді энергияға айналдырады. Серпімді энергияның көлемдік тығыздығы
/2E болады. Үлгіде ұзындығы
көлденең микрожарықшақ пайда болса, үлгі ішінде S еркін бет құрылып, үлгінің энергиясы өседі.
(1. 2. )
мұндағы
- үлгінің еркін беттік энергиясы.
Яғни, үлгіде жарықшақ пайда болғанда оның көлемі серпімділік кернеуінің әсерінен кеміп, серпімділік энергиясы
-ге азаяды. Жарықшақ пайда болуына байланысты үлгі энергиясының жалпы өзгерісі мынадай болады.
(1. 3. )
1 - суретте W-ның жарықшақ ұзындығына тәуелділігі көрсетілген. Ол ең үлкен мәнге
ие болғанда
(1. 4. )
Ең үлкен мәнге сәйкес келетін ұзындықты
деп алсақ, мынаны табамыз:
- дан бастап саңлаудың ұзаруы үлгінің энергиясын азайтады да, морттық күйреуге нақты беріктігін Гриффитс (3) орнына сәйкес былай есептеу керек
(1. 5. )
Бұл нәтиженің дұрыстығы көптеген ғылымдардың зерттеулерінде дәлелденген. Мәселен, мыс үшін:
Equation. 3 болса
Басқа қатты денелер үшін де осы шамалас.
Қатты денелердің беріктігі теориялық мәнінен теханикалық мәніне дейін төмендеу үшін микрожарықшақ пайда болуы керек. Оның пайда болу көздері әртүрлі. Мысалы, ол көптеген ақаулардың қосылуының нәтижесінде пайда бола алады.
1. 2. Қатты денелердің морттық беріктігі
Қатты денелердің күйреуі морттық және пластикалық күйреу болып екіге бөлінеді. Егер
болғанда серпімді деформация кезінде морттық күйреуі болады.
Поляни әдісі:
кернеу түсірілген кристалды үзу үшін атомдардың жазықтықтар арасындағы ара қашықтығын үлкейту керек. Сонда істелетін жұмыс
Бұл энергия жаңадан пайда болған беттердегі энерг
ияға айналады:
- беттік энергия
,
Қатты дененің бір молекулалық қабатының 1 м 2 ауданын буландыру үшін W энергия қажет қатты дененің бір молін буландыру үшін Q энергия қажет. Ол булану жылу сублимациясына тең. Олардың арақатынасы мынадай:
W=Q c m/M (1. 6)
m - қабаттың массасы m=
M - мольдік массасы M=
- молекулалар массасы
- Авагадро саны
- қатты дененің 1 м
2
бетіндегі молекулалар саны. Молекула аралық қашықтық а-ға тең болғанда 1 молекулаға келетін аудан S=a, ал 1 м
2
беттегі молекулалар саны.
Сондықтан
W=Q
c
(
Equation. 3 )
Equation. 3 (1. 7. )
Егер буланған молекулалардың қатты дененің бетімен байланысты a шамаға алыстағанда жоғалтады деп есептесек, онда бір мезгілде осы беттен барлық қабатты алыстатуға керекті күш кернеу мынаған тең:
Қатты дененің теориялық беріктігі дегеніміз осы.
Мысал:
Мұндағы:
- молекула аралық әсерлесу күштерін анықтау.
Қатты дененің теориялық беріктігін молекулалар әсерлесу күштері арқылы есептеу схемасы мынадай: Суретте қатты дененің потенциал энергиясы U(x) оның бөлшектерінің арасындағы өзара әсерлесу күшінің
олардың ара қашықтығына тәуелдік графигі көрсетілген.
- дәл өзгеру заңы белгісіз болғандықтан осы сызықты әр түрлі функциямен өрнектейді.
Кей жағдайда Паляни мен Орован синусойданың жарты бөлігі арқылы өрнектейді. Көлденең қимасы 1 м 2 денені жайлап екі бөлікке айырғанда керекті күш
.
Мұндағы
- 1 м
2
көлденең қимадағы молекулалар саны. (1. 6. ) - теңдікті ескерсек.
(1. 8. )
Мұндағы
қатты дененің теориялық беріктігі. Х ауытқуының өте аз мәндерінде (1. 8. ) - теңдікті былай жазуға болады:
(1. 9. )
Сонымен қатар өте аз ауытқуларда Гук заңы орындалады:
(1. 10. )
(1. 9. ) және (1. 10. ) теңдіктерден
.
1-кестеде серпімділік модулі Е және теориялы беріктік
келтірілген.
1-кесте
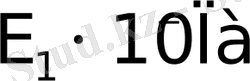
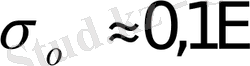
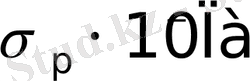
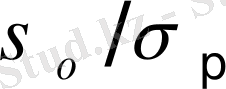




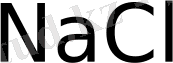
Салыстырғанда үш әдіспен есептелген теориялық беріктікті жуықтап алғанда 0, 1 Е тең. Ал дұрыс есептеуде
1. 3. Қатты денелерді сынау әдістері.
1. 3. 1. Созу деформациясы.
Өте аз уақыт аралығындағы жүктеу кезіндегі өлшеу болып полимердің механикалық қасиеттерінің массалық, техникалық өлшеулері алынды. Бұл топқа созу, сығу, иілу, ығысу, қаттылық сынаулары жатады. Кернеу, деформация, температура және уақыт арасындағы байланыс графиктегі кернеу деформациясы түрінде көрсетіледі. Сынау барысында кернеу және деформация үздіксіз өлшенбейді, сондықтан эксперимент нәтижесі болып салмақ - ығысу диаграмма түрінде анықталады. Осыдан кейін
3-сурет
кернеу және деформация есептелінеді. Көп жағдайда кернеуді бастапқы қимамен есептейді, ал деформацияны үлгінің сынауға дейінгі базалы өлшем шамасына қатысты есептейді.
Осындай өлшеулер нәтежиесінде алынған кернеу - деформация диаграмманың түрі 3-суретте көрсетілген. Әртүрлі деформация түрінде нысанның түрі қисық болғандықтан, қисықты өңдеу, серпімді шаманы, ағын шегін, ығысқан ағын шегін анықтау, үзілетін және максималды кернеу 3-суретте көрсетілгендей бірдей болып қалады. Кернеу-деформация диаграммасының әрбір нүктесі кернеу деформация мәндерінің екі координаталарымен сипатталады.
Әмбебап сынау машиналарында әртүрлі сынау түрлері жүргізіледі. Бұл машиналарды әдетте үзгіш машиналары деп атайды.
Өлшеу аз уақытты жүктеу кезінде сынау жылдамдығы бойынша жүктеледі. Бұл жерде төмен жылдамдықты (
2 м/мин), орташа жылдамдықты (
5 м/с), және жоғарғы жылдамдықты (> 5 м/с) сынауларды атап айтуға болады. Кернеу толқындарының таралу жылдамдығымен жылдамдықтардың жоғарғы шегі анықталады. Осы кезде материалдағы толқынның таралу жылдамдығы әсерлесу жылдамдығынан бірнеше есе үлкен болуы керек. Осы жағдайда кернеу және деформацияның жуық біртекті өрісі үлгіде орнауы мүмкін.
Полимер материалдарда толқынның таралу жылдамдығы, шыныларда 1000 м/с-ге жуық және жоғарғы эластикалық материалдарда 30-50 м/с жылдамдықпен тербеледі. Сондықтан кернеу-деформация диаграммаларының қолдану шегі элестикалық материалдар үшін 10 м/с-тан бастап, ал шыны материалдар үшін бірнеше 100 м/с-қа дейінгі шектерде жатады. Созу кезіндегі өлшеулер жүктеудің басқа түрлеріне қарағанда негізгі орын алады. Созу кезінде материалдың нысаны ғана емес сонымен қатар көлемі де өзгереді. Созуға сынау кезінде қатты материалдарды эластикалық түрге ауыстыру жеңіл жүзеге асады.
Сынаудың созу түрінің артықшылығына материалды үлкен көлемде деформациялаудағы біртекті өріске жетудің қарапайым тәсілі, бір топ материалдан жұқа және жарғақ түрлеріне өтуге мүмкіншіліктің болуы жатады. Созу кезіндегі өлшеулерде материалдардың формалары өзгеріп қана қоймай сонымен бірге материалдарды бағалауда маңызы бар көлем де өзгереді. Созуға сыныу кезінде қатты материалдар иілімді материалдарға оңай өтеді. Бұл айтылғандар кернеу-деформация диаграммасын тіркей отырып өлшеулердің барлық мәселелерін созу мысалдарында қарастыруға мүмкіндік береді.
Тұтқырлы-серпімді денелер үшін кернеу және деформация арасындағы байланысты қарастырғанда циклды деформация кезінде серпімді, ал тұтқырлығы жоқ кезде бұл байланыс түзу сызықты түрде келтірілген, ал кері жағдайда - нысаны дөңгелек түрде болады.
Бұл пайымдаулар өзінің маңызын бір жолға жүктеу кезінде де сақтайды. Мұнда да кернеу - деформация диаграммасының түрі полимер денелердің тұтқырлы - серпімді сипатының кешеніне және полимердің фазалық күйіне айтарлықтай тәуелді.
4-суретте деформацияның әртүрлі температура үшін (а) және жылдамдығы үшін (б) қисықтар шоғы көрсетілген.
4-суретте полиформальдегидтің (а) әртүрлі температура кезіндегі және деформация жылдамдығы кезіндегі (б) кернеу-деформация қисығы.
Қисықтағы цифрлар:
а-суретте температура;
б-суретте деформация жылдамдығы.
Кернеу-деформация қисығын алу кезінде сызықты тұтқырлы серпімділік шегінен шығу себебінің бірі деформация кезінде көлемінің өзгеруімен байланысты. Rusch K. C., Beck R. H., Macromol. Scі., Андрианова Г. П., Каргин В. А., авторлар ағын шегінің кернеу-деформация қисығына тәуелділігін және оның деформация кезінде көлемінің өзгеруімен байланысын орнатты. Кейбір полимерлерде температуралы интервал бар екендігі көрсетілді. Бұл жерде амортты және кристалды полимерлердің қисық нысаны бірдей екендігі көрінеді. Осы жағдай кернеу-деформация қисығын дәл құру қажеттілігін тағы да куәландырады.
Материалдардың қасиеттері жөнінде жалпы мәлімет алу үшін кернеу-деформацияның бастапқы бөлігі ғана емес, сонымен қатар материалдардың беріктік сипаттамалары жөніндегі мәліметтер де қажет.
Салмақ - деформация қисығының екі түрі бар: біріншісі кернеу және деформация (жоғарғы иілімділік күйде) арасындағы пропорционалдықты анықтайтын қисық.
Тепе-теңдік шаманың мәнін химиялық байланыстар торындағы тығыздықты бағалау үшін қолданылады.
Салмақ - деформацияның изохронды қисығы тепе-теңдік қисыққа ұқсас болып келеді. Бұл салмақ - деформацияның изохронды қисықтары 5-суретте көрсетілген.
Изохронды қисықтардың іс жүзінде де (ол бойынша берілген уақыт қорында полимер материалдарының деформацияланғыштығын жобалауға болады), теориялықда да (ол бойынша материалдық сызықты тұтқырлы-серпімді аумағын бағалау, мүмкін болады) айтарлықтай мәні бар.
Серпімділік модулі деформацияға тәуелді болғандықтан,
5-сурет
Поликарбонат үшін үш әртүрлі температуралар кезіндегі кернеу-деформациясының изохронды қисықтары. Қисықтардағы сандар - сағаттағы уақытты база.
әдетте оны 0, 5 пайыздан аспайтын деформация кезінде табады. Кейде модульден өзге деформация мен кернеудің интервалы да анықталады. Онда кернеу деформацияға пропорционал болады. Горизонталь бөлігі бар қисықтар “аққыштық шегі” мен осы нүктеге сәйкес деформацияны анықтайды.
Қисықтарда “аққыштық шегі” болмаған жағдайда, кейбір тәсілдердің талабы бойынша, аққыштықтың ығысқан шегі анықталады. Оны кернеу-деформация қисығы мен қисықтың бастапқы бөлігіне параллель бола отырып берілген деформация шамасын абсцисса өсімен қиып түсетін түзумен қиылысу нүктесі ретінде табады. Әдетте, бұл деформация 0, 1 пайыз бен 2 пайыз аралығында өзгерісте болады.
Созу кезіндегі қасиеттер көрсеткіштерін нысаны мен мөлшері 6-суретте көрсетілгендей үлгілерде анықтайды.
Сынақ жүргізу кезінде үлгіні салқындатады, сынау машиналарының қысқыштарына бекітеді, үлгінің жиегін өлшейді.
6-сурет
Пластмассаларды сынауға арналған үлгілердің үш түрі
1-түрдегі үлгіні иілімділік материалдарды;
2-түрдегі үлгіні қатты материалдарды;
3-түрдегі үлгіні шыны пластиктерді сынау үшін қолданады.
1. 3. 2. Сығу деформациясы
Кернеу-деформация түріндегі механикалық мәліметтерді алудың техникалық өлшеулері созу кезінде ғана емес деформацияның басқа түрлерінде де жүзеге асады. 7-суретте сынау сызбасы көрсетілген, үлгіні сынау үшін арнаулы көмекші лайықталып жабдықталған және параллель орналасқан тіреу плиталар қолданған. Сызу кезінде кернеу-деформация диаграммасы, созылу деформациясы кезінде 3-суреттегі диаграммамен сәйкес келеді. Сонымен бірге төмендегі көрсеткіштерді анықтауға болады. Сығылғандағы кернеудің максимум шегін, кернеудің сығылған кезіндегі бұзылу шегін, сығу кезінде материалдың аққыштық шегін, сығу кезінде аралас аққыштық шегін, пропорционалдық шегін, серпімділік модулін, беріктік модулін, яғни сығылу кезіндегі көрсеткен көрсеткіштер; созылу кезіндегі көрсеткіштерді толығымен қайталап көрсетті.
Сығу кезіндегі кернеу серпімділік күштің, үлгінің бастапқы көлденең қимасының ауданының қатысы арқылы анықталады. Тек кей жағдайда тәжірибе кезінде үлгінің көлденең қимасы өлшенеді және кернеу осыған байланысты салыстырмалы түрде есептеледі. Сығу кезінде күйремейтін заттар үшін кернеуді белгіленген салыстырмалы сығу деформациясы арқылы анықтайды, ол 25 пайызға тең. Бұл өте үлкен деформация. Бұл сығылу кезінде күйретпейтін заттарды анықтауға мүмкіндік береді. бірақ одан кейін бізде белгіленгендей заттың сығуға қарсы тұра алатын шын және аралас аққыштық шегін анықтау қажет. Сығу кезіндегі деформацияның есебін шығару үшін үлгінің ұзындығының кішірейуіне немесе сол сияқты созылу кезіндегі ұзындықтың өзгеруіне, бастапқы кездегі үлгінің ұзындығына байланысты. Деформацияны анықтау салыстырмалы түрде
7-сурет
1 - сынау машинасының тірек плитасы;
2, 7, 9 - мықты орнатылған плиталар;
3 - салмақты стержень;
4 - плунжер;
5 - рама;
6 - шарик;
8 - үлгі
өзгерістен үлгі бастапқы ұзындығының ара қатынасын өлшеумен немесе пайыз есебінде анықтайды. Тәжірибе кезінде заттың аққыштың шегін және күйреу шегін анықтайды. Сығылу кезіндегі деформацияны өте дәлдікпен анықтау үшін үлгінің ұзындығын ұзарту керек, бірақ оған керісінше үлгінің беріктік қасиеті сығылу кезінде жоғары болуы керек. Үлгінің беріктігі сығылу кезінде иілгіштік қасиетімен анықталады.
Радиус инерция табаны квадрат параллелепипед 0, 289-ға тең, таңдап алу заттың серпімділік модуліне байланысты. E>10
3
МПа заттары үшін
Equation. 3 қабылданады. Модулдің кіші мәнінде
Equation. 3 тең. Серпімділік модулді және аралас аққыштық шекті өте дәлдікпен анықтау үшін үлгіні алу керек.
Кейбір жағдайда сығуға тәжірибе жасағанда құбырдан жасалған үлгі қолданылады. Бұл жағдайда үлгінің беріктігі һ құбырдың сыртқы D және ішкі d диаметрлері мына формуламен анықталады.
Equation. 3 (1. 11. )
Сығуға тәжірибе жасағанда стандарт үшін табаны
Equation. 3 мм биіктігі 15 мм немесе 30 мм параллелепипед түрінде, сол сияқты диаметр 10 мм, биіктігі 15 мм немесе диаметрі 12 мм, биіктігі 30 мм цилиндр түрінде алынады.
Үлгілер сығу кезінде төменгі меншікті қаттылығы арқасында ғана емес күш-кернеудің осьтерінің дәлме-дәл келмеуінен де артықтылығын жоғалтады. Сол үшін сығуға сынақ жасағанда жіңішке үлгілердің бойлық орнықтылығын арттыруға арналған арнаулы құрылғылар (8-сурет) және кернеуді оське дәлме-дәл түсіретін құрылғылар (9-сурет) пайдаланылады.
8-сурет
Қалыңдығы 3 мм кем материалдарды сынауға арналған құрылғының сұлбасы
а - үлгінің екі оправканың арасына орналасуы
б - оправканың пішіні
9-сурет
Әдетте, стандарт үлгілерді сынау
Equation. 3 мм/мин жылдамдықпен жүргізіледі, ал қалған үлгілер үшін жылдамдық мына формуламен есептеп табылады:
Equation. 3 (1. 12. )
Мұнда
Equation. 3 - алаңшалардың жақындасу жылдамдығы, мм/мин-пен;
Equation. 3 - үлгінің бастапқы биіктігі, мм-мен.
Сығуға сынау жүргізу кезінде тірек алаңшаларының жақындасуы өте аз болғандықтан, күш өлшегіштің қаттылығына талап күшейеді. Күш өлшегішпен байланысы бар, алаңшаларының ең көп орын ауыстырды 5 мм-ден артатын машиналар қолданылмайды.
Сығу кезіндегі серпімділіктің модулін анықтау тәжірибесі аз деформацияларды өлшеуде, эктензометр үлгінің ұштарына бекітуде қанағаттанарлық нәтижеге жетуге болатынын көрсетеді.
Аққыштық деформациясынан артық деформациялырды анықтау үшін тензометр пайдалану кезінде үлгілердің формасын жоғалтатынын ескеру керек.
Кернеу-деформация диаграммасының берілген нүктедегі қиюшы модулі салыстырмалы бірліктерде кернеудің деформацияға қатынасы ретінде анықталады және кернеудің өлшемділігі бар болады. Егер сығуға тәжірибе жасауда кішкентай үлгілердегі модулді анықтау кезінде пайда болатын қателерді азайту үшін табаны
Equation. 3 мм және биіктігі 6 мм немесе 12 мм мөлшерлі параллелепипед формалы кішкентай үлгілер пайдаланылса, Е серпімділік модулін анықтауды екі үлгіде жүргізу керек және Е-ні мына формуламен есептеп шығару керек:
Equation. 3 (1. 13. )
Сығуға тәжірибе жасаудың созуға қарағанда аз артықшылықтары мен кемшіліктері бар. Артықшылықтарына кішаентай үлгілерді және өлшеуі жеңіл болатын көп күш салуды пайдалана алу, өлшеу кезінде қате мен үлгіні қысқыштарға бекітумен байланысты деформацияның аз болу мүмкіндігі жатады. Кемшіліктерге биік үлгілермен өлшеу жүргізудің мүмкіндігінің болмауы, үлгінің орнықтылығын жоғалту әкелетін қателік, кернеу түсіруде осьтердің дәлме-дәл келуіне талаптық артуы, т. б. жатады. Сығуға сынау жасаудың аталған артықшылықтары материалдар қасиетін инженерлік тұрғыда бағалауға, ғылыми зерттеу жұмыстарын жүргізуде кең өріс алды.
1. 3. 3. Иілу деформациясы
Көптеген морттық материалдарды созуға да, сығуға да сынау қиындық келтіреді; бұл материалдардың деформациялық - беріктік сипатын бағалау үшін иілу кезіндегі сынауды ғана пайдалануға болады. Үлгіні иілуге сынау кезіндегі жүктеудің сұлбасы берілген. 8-суретте мұнда негізгі екі сұлба келтірілген: үш нүктелік (а) және төрт нүктелік (б) кернеу түсіру. Бірінші жағдайда екі тіреуге жататын үлгіге иетін бір ұштықтың көмегімен ортасына жүктеу түсіріледі. Бұл жағдайдағы моменттер эпюрасы үшбұрыш тәрізді болады. Төрт нүктелік жүктеу екі жүктеуші ұштықтың көмегімен іске асырылады (в) моменттер эпюрасы трапеция тәрізді болады. тәсілдер арасындағы негізгі айырмашылықтар үш нүктелік жүктеу кезінде ең үлкен июші момент пен ең үлкен июші кернеулердің бір сызық бойына жинақталуына және төрт нүктелік жүктеу кезінде үлкен ауданға таралуына әкеліп соғады. Үш нүктелік жіктеу негізгі тәсіл болып табылады, ал төрт нүктелік жіктеу әдісі үлгі ұштық жіктеу әсерінен қарқынды үзілетін жағдайда ғана қолданылады. Төрт нүктелік жіктеу үшін D - иілуді есептеу мына формуламен жүргізіледі.
Equation. 3 (1. 14. )
Төрт нүктелік жүктеу үшін D - иілуді есептеу мына формуламен жүргізіледі.
Equation. 3 (1. 15. )
мұндағы:
Equation. 3 - шеткі талшықтарға созу деформациясы
Equation. 3 - тіректер арасының қашықтығы
Equation. 3 -үлгінің қалыңдығы
Максимал кернеу мынаған тең:
Equation. 3 (1. 16. )
мұндағы:
Equation. 3 - үлгілер ортасындағы сыртқы талшықтардағы кернеу
Equation. 3 - нагрузка (салмақ)
Equation. 3 - тірек арасындағы арақашықтық
Equation. 3 - үлгінің ені
Equation. 3 - үлгінің қалыңдығы
Бұл теңдеу күйреуге дейін жеткен деформациямен сызықты байланысты кернеуі бар және деформациясы аз материалдар үшін жарайды. Сондықтан ол пластмассалар үшін орындалмайды. Олар үшін (1. 16) теңдеу бойынша салыстырмалы мақсаттарға пайдалы және
Equation. 3 5 пайыздан кіші болғандағы мәндерді алу үшін шартты шамалар есептен шығарылады. Үлгі тіреулер арасында қысылатын болғанда бұл есептеулер қолданылмайды. Егер тіреулер ара қашықтығы
Equation. 3 үлкен болса, онда ең үлкен кернеулерді есептеу үшін басқа формула пайдаланылады:
10-сурет
Иілуге арналған сынау схемасы.
а - иілгіш үштікпен үлгілерге ортадан салмақ түсіру (үш нүктелік сұлба) ;
б - екі үштікпен үлгілерге салмақ түсіру (төрт нүктелік сұлба) ;
в - төрт нүктелік схема бойынша салмақ түсіругеарналған құрылғы.
Equation. 3 (1. 17. )
мұндағы: D - қысқыштар арасындағы үлгінің орталық сызығының майысуы.
... жалғасы- Іс жүргізу
- Автоматтандыру, Техника
- Алғашқы әскери дайындық
- Астрономия
- Ауыл шаруашылығы
- Банк ісі
- Бизнесті бағалау
- Биология
- Бухгалтерлік іс
- Валеология
- Ветеринария
- География
- Геология, Геофизика, Геодезия
- Дін
- Ет, сүт, шарап өнімдері
- Жалпы тарих
- Жер кадастрі, Жылжымайтын мүлік
- Журналистика
- Информатика
- Кеден ісі
- Маркетинг
- Математика, Геометрия
- Медицина
- Мемлекеттік басқару
- Менеджмент
- Мұнай, Газ
- Мұрағат ісі
- Мәдениеттану
- ОБЖ (Основы безопасности жизнедеятельности)
- Педагогика
- Полиграфия
- Психология
- Салық
- Саясаттану
- Сақтандыру
- Сертификаттау, стандарттау
- Социология, Демография
- Спорт
- Статистика
- Тілтану, Филология
- Тарихи тұлғалар
- Тау-кен ісі
- Транспорт
- Туризм
- Физика
- Философия
- Халықаралық қатынастар
- Химия
- Экология, Қоршаған ортаны қорғау
- Экономика
- Экономикалық география
- Электротехника
- Қазақстан тарихы
- Қаржы
- Құрылыс
- Құқық, Криминалистика
- Әдебиет
- Өнер, музыка
- Өнеркәсіп, Өндіріс
Қазақ тілінде жазылған рефераттар, курстық жұмыстар, дипломдық жұмыстар бойынша біздің қор #1 болып табылады.

Ақпарат
Қосымша
Email: info@stud.kz