ТЕХНОЛОГИЧЕСКИЕ МАШИНЫ И ОБОРУДОВАНИЕ ДЛЯ ГЛУБОКОЙ ПЕРЕРАБОТКИ РАСТИТЕЛЬНОГО СЫРЬЯ


МИНИСТЕРСТВО СЕЛЬСКОГО ХОЗЯЙСТВА
НАО «Казахский агротехнический университет имени С. Сейфуллина»
К. С. БЕКБАЕВ, С. Д. ТОКАЕВ, А. ТӨЛЕУҒАЗЫҚЫЗЫ
ТЕХНОЛОГИЧЕСКИЕ МАШИНЫ И ОБОРУДОВАНИЕ ДЛЯ ГЛУБОКОЙ ПЕРЕРАБОТКИ РАСТИТЕЛЬНОГО СЫРЬЯ
Учебно-теоретическое издание
Нур-Султан, 2021
МИНИСТЕРСТВО СЕЛЬСКОГО ХОЗЯЙСТВО
РЕСПУБЛИКИ КАЗАХСТАН
Казахский агротехнический университет имени С. Сейфуллина
К. С. БЕКБАЕВ, С. Д. ТОКАЕВ , А. ТӨЛЕУҒАЗЫҚЫЗЫ
ТЕХНОЛОГИЧЕСКИЕ МАШИНЫ И ОБОРУДОВАНИЕ ДЛЯ ГЛУБОКОЙ ПЕРЕРАБОТКИ РАСТИТЕЛЬНОГО СЫРЬЯ
Нур-Султан 2021
УДК 622. 014. 5: 667. 621. 428
ББК 30. 6:34. 5
К30
К. С. Бекбаев, С. Д. Токаев, А. Төлеуғазықызы. Технологические машины и оборудование для глубокой переработки растительного сырья. Учебное пособие. - Нур-Султан: Казахский агротехнический университет имени С. Сейфуллина, 2021. - 200.
Учебное пособие содержит сведения о назначении, классификации, устройстве и принципе действия основного оборудования для ведения химических и биотехнологических процессов при глубокой переработке с. х. сырья.
Рецензенты:
Ф. И. О. рецензента, асс. профессор, к. т. н. Б. Б. Кабулов
Ф. И. О. рецензента, доцент, к. т. н. М. М. Какимов
Учебное пособие предназначено для обучающихся высших учебных заведений, для использования в качестве руководства по курсу машины и оборудования перерабатывающего производства.
© К. С. Бекбаев, С. Д. Токаев, А. Төлеуғазықызы. 2021
© Казахский агротехнический университет имени С. Сейфуллина, 2021.
СОДЕРЖАНИЕ
Предисловие
Учитывая огромное многообразие оборудования для переработки растительного сырья, авторы посчитали целесообразным включить в состав учебного пособия главы, отражающие последовательность разработки оборудования, основную элементную базу машин и аппаратов.
Для более полного понимания физической сущности происходящих процессов в машине или аппарате авторы посчитали необходимым давать краткую характеристику протекающих в оборудовании процессов, связывая параметры процесса с качеством работы оборудования и его производительностью.
Машины и оборудование, применяемые при ведении химических биотехнологических процессов, значительным образом влияют на их качество и эффективность. Только изучение конструкции и принципа действия указанного оборудования позволит в дальнейшем повысить качество работы оборудования на основе их усовершенствования, а, следовательно, абсолютно точно обеспечить режимы протекания биотехнологических процессов.
Глава І Общие сведения об оборудовании для глубокой переработки растительного сырья
- Классификация оборудования
Под классификацией оборудования в общем случае понимают научно-обоснованное распределение машин и аппаратов по отдельным группам на основе определенных признаков, важнейшими из которых для перерабатывающего оборудования являются: производственное назначение, проводимый в машинах или аппаратах процесс, функциональное назначение, принцип организации технологического процесса, степень автоматизации и т. д.
Оборудование перерабатывающего производства в зависимости от его производственного назначения подразделяют на следующие классы: технологическое, энергетическое, транспортное, ремонтное, грузоподъемное и вспомогательное. В данном учебном пособии рассматривается только технологическое и вспомогательное оборудование. Остальное перечисленное оборудование является предметом специальной литературы.
Технологическое оборудование предназначено для реализации различных технологических процессов производства.
Технологическое оборудование по характеру протекающих в нем процессов подразделяется на следующие классы: оборудование для механических процессов; оборудование для гидромеханических процессов; оборудование для тепловых процессов; оборудование для массообменных процессов; оборудование для химических процессов.
Внутри каждого класса оборудование подразделяется по функциональному назначению на группы.
Оборудование для механических процессов по функциональному назначению подразделяется на грохоты, классификаторы, дробилки, мельницы, смесители, питатели, дозаторы.
К оборудованию для гидромеханических процессов относятся отстойники, центрифуги, сепараторы, гидроциклоны, циклоны, скрубберы, фильтры, электрофильтры, аппараты для механического и циркуляционного перемешивания жидких сред и т. д.
Оборудование для тепловых процессов включает в себя рекуперативные, регенеративные и контактные теплообменники, тепловые трубы, тепловые печи, плазматроны, а также выпарные и кристаллизационные аппараты.
К оборудованию для массообменных процессов относятся абсорбционные и ректификационные колонны, экстракционные аппараты, адсорберы, ионообменные аппараты, аппараты для баромембранных и диффузионных процессов, сушилки, аппараты для растворения и выщелачивания и др.
К оборудованию для проведения химических процессов относятся химические реакторы и печи для осуществления химических процессов и др.
Кроме того, каждая группа оборудования подразделяется на типы, а типы - на типоразмеры.
Вспомогательное оборудование предназначено для реализации в нем вспомогательных процессов производства, в частности, хранения и транспортировки жидкостей, сжиженных газов, паров и газов, сыпучих материалов в требуемом для технологического процесса направлении. К вспомогательному оборудованию перерабатывающих производств относятся: резервуары для хранения жидкостей и сжиженных газов, газгольдеры, бункеры и силосы для сыпучих материалов и др.
Технологическое оборудование по характеру воздействия на сырье или полуфабрикаты может быть разделено на аппараты и машины.
Аппаратом называют инженерное сооружение, несущее в себе реакционное пространство (рабочий объем) и снабженное энергетическими и контрольно-измерительными средствами ведения и управления технологическим процессом.
Реакционное пространство (рабочий объем) - пространство, в котором осуществляется технологический процесс.
В случае, если проведение технологического процесса сопровождается вводом в рабочий объем механической энергии за счет рабочих органов оборудования, то такой аппарат называется машиной.
Машины и аппараты по принципу организации технологического процесса подразделяются на оборудование непрерывного и периодического действия.
Машины и аппараты непрерывного действия характеризуются тем, что основные стадии (операции) технологического процесса осуществляются в разных рабочих объемах оборудования, но в одно и то же время. Как правило, машины и аппараты непрерывного действия менее металло- и энергоемки, отличаются простотой конструкции и высокой удельной производительностью.
В машинах и аппаратах периодического действия основные стадии (операции) технологического процесса осуществляются в одном и том же рабочем объеме, но в разное время. Основное достоинство оборудования периодического действия - большая технологическая гибкость, т. е. возможность быстрого перехода с одного вида продукции на другой с минимальными затратами времени без снижения качества продукции.
По степени автоматизации технологические машины можно разделить на следующие группы:
- простые - машины, с помощью которых человек-оператор совершает заданные технологические операции по программе, которую «держит в голове»;
- полуавтоматические (автоматизированные) - машины, которые выполняют основные технологические операции согласно заложенной в них программе без непосредственного участия оператора, в функции которого входят лишь загрузка, разгрузка, контроль и регулирование машины:
- автоматические - машины, выполняющие после загрузки и выключения все рабочие операции по заданной программе без участия оператора (машина-автомат) .
Если машина-автомат обладает способностью производить логические операции, вырабатывать и осуществлять в соответствии со своим целевым назначением программу действия с учетом переменных условий протекания технологического процесса, то она называется самонастраивающейся.
1. 2 Требования, предъявляемые к оборудованию для глубокой переработки растительного сырья
Показатели качества и особенности условий эксплуатации оборудования по глубокой переработке сырья растительного происхождения. Эффективность и современный технический уровень машин и аппаратов перерабатывающих производств, как и любого другого вида промышленной продукции, определяются следующими группами показателей качества, характеризующими основные свойства оборудования (ГОСТ 22851) . Показатели качества являются важным элементом, формирующим требования к конструкции машин и аппаратов.
Стандарт устанавливает следующую номенклатуру основных групп показателей качества.
1. Показатели назначения характеризуют свойства оборудования, определяющие основные функции, для выполнения которых оно предназначено (производительность, энергозатраты, скорости рабочих органов, мощность, усилия и др. ) .
2. Показатели надежности, характеризующие свойства безотказности, долговечности, ремонтнопригодности и сохраняемости.
3. Эргономические показатели характеризуют систему «человек-изделие» и учитывают комплекс гигиенических, антропометрических, биомеханических, физиологических и психологических свойств человека, проявляющихся в производственных условиях.
4. Эстетические показатели характеризуют информационную выразительность, рациональность формы, целостность композиции и совершенство производственного исполнения оборудования.
5. Показатели технологичности характеризуют свойства оборудования, обуславливающие оптимальные затраты материалов, средств труда и времени при изготовлении данного оборудования.
6. Показатели транспортабельности характеризуют приспособленность оборудования к перемещению в пространстве. Такими показателями являются, в частности, средние продолжительность и трудоемкость подготовки оборудования к транспортированию, средняя продолжительность установки изделия на средство транспортирования, коэффициент использования его объема и др.
7. Показатели стандартизации и унификации характеризуют насыщенность оборудования стандартными, унифицированными и оригинальными элементами, отражают степень использования стандартных и однотипных узлов и деталей в данном изделии.
8. Патентно-правовые показатели характеризуют степень обновления технических решений, использованных во вновь спроектированном оборудовании, их патентную защиту, а также возможность его беспрепятственной реализации в России и за рубежом.
9. Экологические показатели определяют уровень вредных воздействий на окружающую среду при эксплуатации оборудования. К таким показателям относятся, например, содержание вредных примесей, выбрасываемых в окружающую среду, вероятность выброса вредных частиц, газов, излучений при хранении, транспортировании, эксплуатации оборудования и т. д.
10. Показатели безопасности характеризуют особенности оборудования, обуславливающие безопасность обслуживающего персонала при транспортировании, монтаже, эксплуатации, хранении; это, например, вероятность безотказной работы, время срабатывания защитных устройств и ряд других показателей.
В зависимости от стадии определения различают показатели качества прогнозируемые, т. е. указанные в техническом задании на проектирование оборудования; проектные, т. е. найденные в результате проведения расчетно-конструкторских работ; производственные, т. е. полученные при контрольных испытаниях оборудования, и эксплуатационные, т. е. соответствующие условиям эксплуатации оборудования на конкретных предприятиях.
КОНТРОЛЬНЫЕ ВОПРОСЫ
1. Какие функциональные типы машин образуют класс оборудования для проведения механических процессов?
2. Какие функциональные типы машин и аппаратов образуют класс оборудования для проведения гидродинамических процессов?
3. Дайте определение понятий «машина» и «аппарат».
4. Какое основное отличие технологического оборудования непрерывного действия от оборудования периодического действия?
5. Что входит в понятие «самонастраивающаяся машина - аппарат»?
6. Перечислите показатели качества, характеризующие основные свойства оборудования.
7. Какие наиболее существенные климатические факторы необходимо учитывать при проектировании технологического оборудования, предназначенного для установки на открытых площадках?
8. Приведите основные требования, предъявляемые к вновь разрабатываемому технологическому оборудованию.
9. Дайте характеристику основным этапам разработки технической документации при проектировании оборудования.
Глава ІІ Оборудование для механической обработки сырья
Процесс механического воздействия реализуется в результате нагружения кусков либо частиц тела, что ведет к появлению критических внутренних напряжений, превышающих соответствующий предел прочности. Напряжения в материале могут создаваться механическим нагружением, температурными воздействиями, ультразвуковыми колебаниями и др. Наибольшее применение в современном производстве имеют механические способы измельчения.
2. 1 Характеристика основных способов и машин для измельчения
Измельчение делят на дробление и помол, а машины, применяемые для этих целей, называются дробилками и мельницами. В зависимости от размеров частиц продукта (конечного размера частиц d K ) различают следующие виды измельчения: дробление крупное (d K =100 . . . 350 мм ), среднее (d K =40 . . . 100 мм ), мелкое (d K =5 . . . 40 мм) , помол грубый (d K =0, 1 . . . 5 мм) , средний (d K =0, 05 . . . 0, 1 мм) , тонкий (d K =0, 001 . . . 0, 05 мм) , сверхтонкий (d K <0, 001 мм) .
Основной характеристикой процесса измельчения является степень измельчения, которая определяется соотношением средневзвешенных размеров частиц материала до (d н ) и после (d K ) измельчения
i 0 =d н /d K
Степень измельчения отражает технологию и параметры измельчителей.
С целью обеспечения эффективности и минимизации затрат измельчение материала от исходной до конечной крупности осуществляется, как правило, в несколько приемов, с последовательным переходом от крупного дробления к более мелкому и к помолу с постадийным разделением материала по классам. Следовательно, процесс измельчения целесообразно осуществлять последовательно на . Каждый отдельный измельчитель выполняет часть общего процесса, называемую стадией измельчения.
Число стадий измельчения определяется требуемой степенью измельчения. Например, если в исходном твердом материале содержатся куски размером до 1200 мм, а готовый продукт должен содержать частицы с максимальным размером до 40 мм, то общая степень измельчения i 0 =1200/40=30 .
Степень измельчения, достигаемая на одной машине, для большинства видов дробильного оборудования не превышает 5 . . . 50. Поэтому для обеспечения i 0 =300 необходимо применить несколько стадий дробления, например: i 1 =5 , i 2 =6 , i 3 =10 . Тогда i 0 =i 1 ·i 2 ·i 3 =5·6·10=300 , т. е. требуется минимум три стадии измельчения.
В то же время следует отметить, что увеличите стадий измельчения приводит к переизмельчению материала и увеличению эксплуатационных затрат. Поэтому процесс следует осуществлять, исходя из условия обеспечения минимального числа стадий измельчения.
Энергозатраты, нагрузки на элементы измельчителей и качество продукта зависят от физико-механических характеристик материала: прочности, хрупкости, твердости, упругости, абразивности и плотности твердых материалов.
В зависимости от размера частиц, например от эквивалентного (среднего) диаметра d, твердый материал может быть в следующих состояниях: кусковом (d>10 мм) ; крупнозернистом (2 мм<d<10 мм) ; мелкозернистом (0, 5мм<d<2 мм) ; порошкообразном (0, 05 мм<d<0, 5 мм) ; пылевидном (d<0, 05 мм) .
Для оценки полидисперсной смеси твердых частиц используются следующие характеристики:
- наибольший d max и наименьший d min диаметры частиц;
- размах варьирования R=d max d min ;
- средний диаметр частиц d;
- гранулометрический состав;
- удельная поверхность частиц S у .
Классификация машин для измельчения материалов
В зависимости от назначения и принципа действия в машинах для измельчения могут использоваться различные виды нагрузок: раздавливание (сжатие куска), излом (изгиб), раскалывание (эквивалентно растяжению), истирание и удар (рис. 2. 1) . В каждой измельчающей машине реализуются, как правило, все способы измельчения, но главную роль играет тот, для которого она создана.
При раскалывании тело разрушается на части в местах концентрации наибольших нагрузок, передаваемых клинообразным рабочим элементом измельчителя.
При раздавливании - под действием статической нагрузки определяющими являются напряжения сжатия.
При изломе в теле возникают в основном изгибающие напряжения.
При истирании разрушение происходит главным образом от напряжений сдвига. Истирание в комбинации с раздавливанием - один из наиболее экономичных способов измельчения.
При ударе под действием динамических нагрузок в теле возникают динамические напряжения, приводящие к его разрушению. Различают свободный и стесненный удары. При стесненном ударе тело разрушается между двумя рабочими органами измельчителя, при свободном - в результате столкновения с рабочим органом или другим измельчаемым телом.
Рис. 2. 1 - Способы механического разрушения материалов, реализуемые в дробилках и мельницах:
>- преобладающие; >- сопутствующие
Как правило, перечисленные виды силовых нагрузок в процессе измельчения действуют одновременно, например, раздавливание и истирание, удар и истирание и т. д. Необходимость в различных видах нагрузок, а также в различных по принципу действия конструкциях и размерах машин вызвана многообразием свойств и размеров измельчаемых материалов и различными требованиями к крупности исходного материала и готового продукта. Однако при работе измельчителей в зависимости от их конструкций преобладает тот или иной способ измельчения.
Имеются практические рекомендации по использованию соответствующих видов нагрузок в зависимости от типа измельчаемого материала. Так, дробление прочных и хрупких материалов целесообразно осуществлять раздавливанием и изломом, а прочных и вязких - раздавливанием и истиранием. Крупное дробление мягких и хрупких материалов предпочтительно выполнять раскалыванием, среднее и мелкое - ударом. В промышленности дробление материалов проводят, как правило, сухим способом.
Реже применяют мокрое дробление, когда в загрузочные устройства машин разбрызгивают воду для уменьшения пылеобразования, либо дробление производится в жидкости с помощью движущихся в ней твердых частиц (бисера) .
Помол твердых материалов осуществляют ударом и истиранием. Так же как и дробление, помол может быть сухим и мокрым. По сравнению с сухим, мокрый помол экологически более совершенен и более производителен. Однако мокрый помол может применяться только тогда, когда допускается контакт измельчаемого материала с водой.
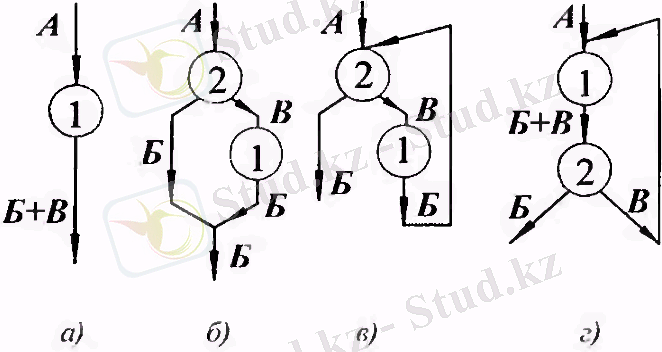
Рис. 2. 2 - Технологические схемы измельчения: а - открытый цикл; б -открытый цикл с предварительным грохочением; в -замкнутый цикл с совмещенным предварительным и поверочным грохочением; г -замкнутый цикл с грохочением.
Процессы: 1- дробление; 2 -грохочение.
Потоки: А - исходный материал; Б - мелкая фракция; В -крупная фракция
При проектировании схем измельчения любых материалов необходимо соблюдать принцип «не измельчать ничего лишнего», поскольку переизмельчение приводит к излишнему расходу энергии, снижению производительности и росту износа дробилок и мельниц. Материалы высокой и средней крепости дробятся, как правило, в две-три стадии, более мягкие - в одну стадию.
В перерабатывающей промышленности применяются в основном одностадийные технологические системы измельчения, которые представлены на рис. 2. 2. Открытая система (рис. 2. 2 а) применяется при крупном измельчении (до 20 мм) . В замкнутых системах с классификатором (грохотом) (рис. 2. 2 б-г) крупность продукта можно дополнительно регулировать с помощью грохота.
По способу воздействия на измельчаемый материал различают дробилки, разрушающие материал сжатием (щековые, конусные и валковые дробилки) и ударом (роторные и молотковые дробилки) .
По конструктивным признакам различают дробилки: щековые, валковые, конусные, ударного действия (роторные и молотковые) . Пальцевые измельчители и бегуны занимают промежуточное положение между дробилками и мельницами, так как их можно применять как для мелкого дробления, так и для крупного помола.
... продолжение- Информатика
- Банковское дело
- Оценка бизнеса
- Бухгалтерское дело
- Валеология
- География
- Геология, Геофизика, Геодезия
- Религия
- Общая история
- Журналистика
- Таможенное дело
- История Казахстана
- Финансы
- Законодательство и Право, Криминалистика
- Маркетинг
- Культурология
- Медицина
- Менеджмент
- Нефть, Газ
- Искуство, музыка
- Педагогика
- Психология
- Страхование
- Налоги
- Политология
- Сертификация, стандартизация
- Социология, Демография
- Статистика
- Туризм
- Физика
- Философия
- Химия
- Делопроизводсто
- Экология, Охрана природы, Природопользование
- Экономика
- Литература
- Биология
- Мясо, молочно, вино-водочные продукты
- Земельный кадастр, Недвижимость
- Математика, Геометрия
- Государственное управление
- Архивное дело
- Полиграфия
- Горное дело
- Языковедение, Филология
- Исторические личности
- Автоматизация, Техника
- Экономическая география
- Международные отношения
- ОБЖ (Основы безопасности жизнедеятельности), Защита труда